ИНСТРУМЕНТЫ ОПТИМИЗАЦИИ ПРОИЗВОДСТВЕННЫХ ПРОЦЕССОВ. ПОВЫШЕНИЕ ЭФФЕКТИВНОСТИ РАБОТЫ И ВОВЛЕЧЕННОСТИ ПЕРСОНАЛА ЭКСПЛУАТАЦИОННЫХ И РЕМОНТНЫХ ПОДРАЗДЕЛЕНИЙ
Для кого:
- для руководителей и специалистов финансовых служб,
- бухгалтерских служб предприятий и их обособленных подразделений,
- финансовых директоров,
- заместителей по экономике,
- всех заинтересованных специалистов.
ПРОГРАММА
Первый день
- Управление эффективностью компании. Компоненты системы Business Performance Management (BPM)
- Генераторы увеличения стоимости компании в зоне ответственности производственного и ремонтного персонала
- Определение оптимальной модели предприятия и выбор производственной стратегии
- Факторы, определяющие производственную структуру предприятия
- Процессная модель производственного предприятия
Практикум: Слушатели разработают план инициатив направленных на эффективную реализацию производственного и технического потенциала предприятия
Направления (программы) повышения эффективности производственного процесса
- Влияние производственного процесса на увеличение оборота (выручки) предприятия
- Программы сокращения затрат и минимизации потерь.
В чем разница? Примеры программ сокращения затрат
- Инициативы, направленные на эффективное использование активов
- Повышение управляемости производственного процесса
Системы управления материальными потоками в производстве. Преимущества и недостатки каждой из систем
- Толкающая (push) система. Цели, содержание, достоинства, недостатки
- Производственное планирование в Push – системах
- Планирование потребности в материалах (MRP — Material Requirements Planning), планирование ресурсов производственного предприятия (MRPII — Manufactory Resource Planning)
- Производственное планирование: синхронное планирование и оптимизация (APS — Advanced Planning and Scheduling System, MES — Manufacturing Execution System)
- Вытягивающая (pull) система. Цели, содержание, достоинства, недостатки
- Производственное планирование в pull – системах.
- Система Канбан
- Cистема JIT
Современные западные и отечественные подходы управления активами, производственными фондами:
- Требования стандартов серии ISO 9001-2015 к управлению инфраструктурой и производственным процессам, процессов технического обслуживания и ремонта(ТОиР)
- Процессный подход — один из основных принципов менеджмента качества
- Уровни зрелости процессов.
Вовлеченность персонала в процесс улучшения и оптимизации процессов
- Модель процесса. Сеть процессов
- Матрица взаимосвязи процессов
- Карта процесса
- Блок-схема процесса
- Анализ направлений оптимизации, возможных проектов ускорителей на производстве
Практикум: Слушатели разработают несколько схем процессов
Требования стандартов серии ISO 55000:2014 к системе управления (менеджмента) активами:
- Состав, цели, структура, содержание, область применения стандартов серии ISO 55000:2014
- Структура, стратегия, цели, стратегический план управления активами
- Анализ модели управления активами по предметным областям
- Риск-менеджмент для управления портфелем активов
Практикум: Слушатели разработают систему сбалансированных показателей, направленных на увеличение фондоотдачи от производственных фондов своего предприятия
Взаимодействие структурных подразделений предприятия при создании ценности
Интегрированная система повышения эффективности производства, основные концепции
Сущность и принципы «Теории ограничения систем» (ТОС)
- Ограничение и его влияние на деятельность предприятия
- Эффективная производительность
- Финансовые показатели ТОС
- «Буфер» — «барабан» — «веревка»
- Методика «расшивки узких мест»
Практикум: Слушатели проведут анализ применения ТОС на своих участках
QRM–manufacturing.
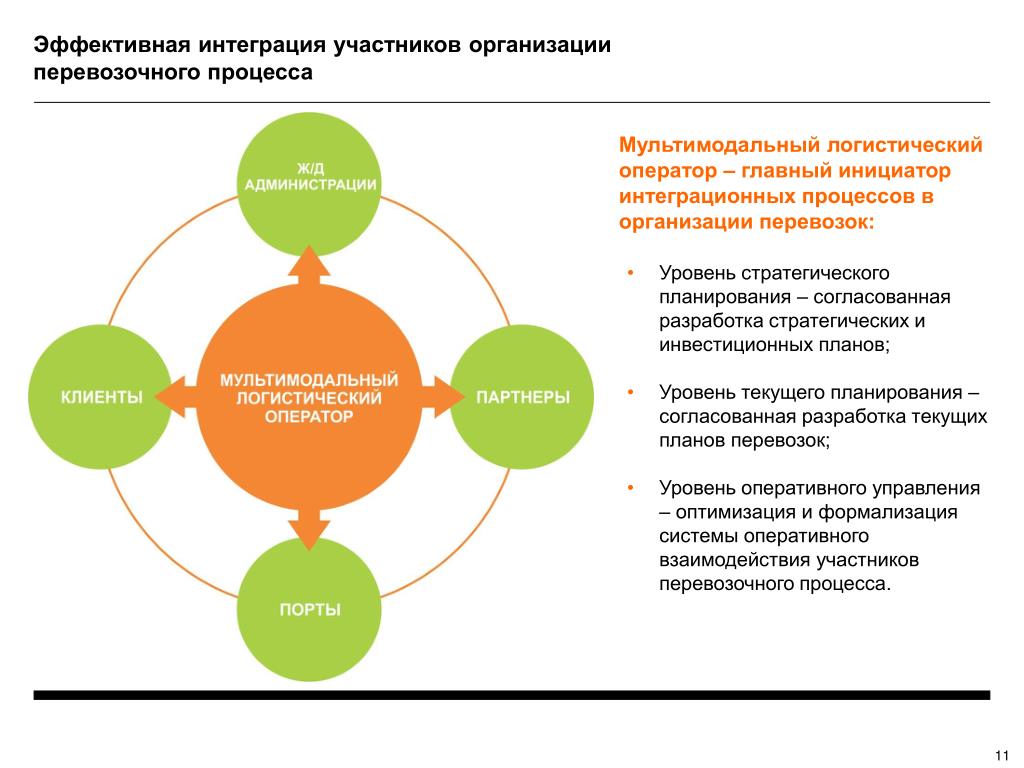
- Стратегия QRM
- Принципы быстрореагирующего производства
- Совместное использование QRMи Leanproduction
Второй день
ЕАM – методология управления основными фондами предприятия
- Основные бизнес-процессы и показатели управления ТОиР
- Организация учета оборудования, показателей эксплуатации. Определение критичных объектов
- Особенности планирования и бюджетирования ТОиР.
- Управление материально-техническим обеспечением ТОиР. Управление складскими запасами, обеспечивающими выполнение ремонтной программы.
- Управление персоналом
- Анализ функциональности зарубежных и российских информационных ЕАМ – систем
- Повышение производительности эксплуатационного и ремонтного персонала на базе решений SAP
Практикум: Слушатели разработают показатели результативности процессов ТОиР для своих подразделений
Выбор стратегии организации ремонтов и обслуживания оборудования (концепции проведения ТОиР)
- Классификация стратегий и методов организации ремонтов
- Планово-предупредительные ремонты (вне зависимости от состояния оборудования)
- Ремонты по отказам (аварийные ремонты)
- Ремонты по диагностике (фактическому состоянию)
- Ремонты, ориентированные на надежность (RCM)
Практикум: Разработка комплексной стратегии организации ТОиР
Бюджет на обслуживание и ремонт
- Основные принципы бюджетирования ТОиР
- Объектное планирование ремонтного фонда.
Как планируются бюджеты материально – технического снабжения в целях выполнения всех видов ремонтов? Опыт управления складскими запасами зарубежных и российских предприятий
- Технико – экономическое планирование мероприятий ТОиР
- Управление бюджетом, программы сокращения затрат
Практикум: Внедрение проекта «Минимизация складских запасов». План мероприятий по снижению неликвидных запасов
Опыт использования ресурсосберегающих технологий «бережливое производство» зарубежными и отечественными предприятиями
Система постоянных улучшений Кайдзен
- Ключевые принципы Кайдзен
- Организация постоянного совершенствования процессов
Оптимизация и стандартизация бизнес и производственных процессов, процедур
- Принципы стандартизации процессов
- Рассмотрение этапов стандартизации процессов: моделирование, регламентация, аудит, оптимизация
- Шесть SIGMA.
Cструктурированный подход оптимизации процессов – DMAIC
- Инструмент определения неэффективности процесса – ГЕМБА
- Описание процессов на базе диаграммы SIPOC
Практикум: Оптимизация процесса «Наставничество» на базе технологии SIPOC
Борьба с основными видами потерь. Программы сокращения затрат
- Анализ видов потерь
- Организация работы рабочих групп по оценке и минимизации потерь
- Анализ инструментов, направленных на минимизацию потерь
- Примеры инициатив по борьбе с потерями реализованные мировыми лидерами
Система организации и рационализации рабочих мест 5S на производстве и в офисе
- Принципы построения системы организации и рационализации рабочих мест 5S
- Эффект от внедрения системы 5S
- Этапы внедрения системы 5S
- Анализ проектов по организации и рационализации рабочих мест 5S, реализованных мировыми лидерами
Практикум: Выход на производство – разработка плана внедрения системы 5S у заказчика
Система всеобщего обслуживания оборудования – ТРМ
- Цели, задачи, принципы TPM
- Направления развертывания TPM
- Направления развертывания самостоятельного обслуживания оборудования
- Структура потерь на оборудовании
- Полная эффективность оборудования (ОЕЕ)
- Инструмент быстрой переналадки (SMED)
- 7 этапов освоения автономного обслуживания
Практикум: упражнение «Расчет эффективности использования оборудования»
Эффективное управление потоком создания ценности
- Общая схема реализации потока — концепция TFM (Totalflowmanagement)
- Ячеистая структура производства
- Многостаночное обслуживание
- Система вытягивания Канбан
- Картирование потока создания ценности VSM (Valuestreammapping)
- Стандартизация – инструмент повышения эффективности потока создания ценности
Методы решения проблем, снижающих эффективность производства
- Алгоритм успешного решения проблем 8D
- 1D – Описание проблемы
- 2D – Формирование команды
- 3D – Определение проблемы
- 4D – Отображение причин
- 5D – Сбор данных
- 6D – Мозговой штурм
- 7D – Проведение критического анализа
- 8D – Планирование и мониторинг
Третий день
Технология эффективного управления производственным коллективом
- Функции и задачи руководителя на производственном участке
- Методы оперативного управления в производственной деятельности
- Распределение функциональных обязанностей, ответственности и полномочий
- Методы постановки задач перед подчиненными и контроль результатов
- Делегирование задач.
Преимущества, риски и типичные ошибки делегирования
- Манипуляции персонала
- Методы управленческого воздействия, методы контроля
Практикумы:
- Слушатели разработают матрицу распределения компетенций для своих подразделений
- Слушатели рассмотрят кейс «Проблемы, снижающие эффективность работы, определение приоритетных путей их решения»
Повышение эффективности производственного процесса в цехе и на участке
- Формирование бригад и их расстановка
- Модели подачи материалов
- Эффективная подача материалов в цех и на участок — система Канбан
Мировой опыт разработки систем управления эффективностью персонала
- Проблемы повышения эффективности персонала. Как научить персонал работать? Как раскрыть инициативу своих сотрудников, какие для этого необходимы условия?
- Анализ систем мотивации персонала применяемых мировыми компаниями.
Достоинства и недостатки
- Что лучше наказывать за нарушения или поощрять за выполнение задач подразделений, групповых или личных показателей
- Подход повышения эффективности персонала компании McKinsey
- Структура конкурентного компенсационного пакета
- Примеры компенсационных пакетов ведущих мировых предприятий
Практикум: Разработка структуры конкурентного компенсационного пакета для предприятия слушателей
Принципы разработки системы мотивации на базе KPI (Key Performance Indicator)
- За что платить постоянную и переменную часть заработной платы
- От чего зависит соотношение постоянной и переменной части заработной платы
- Разработка политики формирования переменной части заработной платы
- Каким образом организовать постановку целей, задач, разработку личных и групповых показателей эффективности. Кто должен этим заниматься?
- Характеристика KPI.
Виды KPI. Целевые уровни, веса KPI. Рекомендуемое количество KPI для подразделений, групп сотрудников
- Развертывание стратегических целей на уровень цеха / участка
- Ключевые показатели эффективности (KPI). Система оплаты труда на основе KPI
- Примеры использования KPI для повышения эффективности персонала различных подразделений
Что эффективнее — система мотивации на базе KPI или повышение вовлеченности персонала?
- Основы стратегии вовлеченности персонала
- Уровни приверженности к компании
- Согласованность. Организация работы кросс-функциональных команд, проектных команд, рабочих групп
- Коммуникации (рабочие группы, кайдзен, доступные инструменты внедрения изменений, снижение внутренней дезориентации)
- Расширение полномочий
- Раскрытие инициативы персонала (возможность предлагать улучшения, оптимизацию процессов, рац. предложения, признание)
- Развитие самодисциплины
- Оценка вовлеченности персонала
Использование методик международных стандартов серии ISO 9000, ToyotaProduction, SixSigma в целях раскрытия потенциала персонала
- Принципы и программы повышения вовлеченности персонала
- Программы постоянного улучшения.
Примеры реализации программ на предприятиях
- Направления оптимизации бизнес – процессов. Критерии оптимизации. Примеры оптимизации производственных процессов
- Организация оптимизации производственных процессов с помощью Стандартных Операционных Процедур (СОП). Примеры СОП. Принципы разработки СОП. Разработка программы внедрения СОП на предприятии
- Наставничество. Виды наставничества. Примеры внедрения. Использование СОП в целях передачи опыта, развития наставничества
- Программы сокращения затрат, программы минимизации потерь. Примеры программ сокращения затрат «спущенных сверху» и разработанных «снизу»
- Бережливое производство.Бережливый офис. Примеры программ
- Примеры организации работы групп функционального совершенства, оптимизации процессов, сокращения затрат организованные на предприятиях лидерах
Практикум: Слушатели разработают программы оптимизации бизнес-процессов, программы постоянного улучшения, направленные на сокращение затрат и возможных потерь
В результате проведения семинара будет сформирована для предприятия Заказчика программа повышения эффективности производства, повышения эффективности персонала, назначены ответственные исполнители
В дополнение к трём дням обучения возможно проведение ещё двух дней для реализации методик, подходов, написания планов, аудита на местах Заказчика.
УДОСТОВЕРЕНИЕ О ПОВЫШЕНИИ КВАЛИФИКАЦИИ ПО ОКОНЧАНИИ КУРСА
В конце учебного курса будет проведена итоговая аттестация. Участники, прошедшие итоговую аттестацию, получат удостоверение о повышении квалификации.
Оптимизация производственных процессов в Anheuser-Busch InBev
Компания использовала Minitab® Statistical Software для анализа собранных данных. Выделенная проектная группа реализовала проект по методологиям бережливого производства и «Шесть сигм», который не только снизил простои и сэкономил средства, но и предоставил решение, которая компания могла масштабировать во всем мире для повышения эффективности бизнеса.
О компании
Anheuser-Busch InBev – крупнейшая в мире пивоваренная компания, ведущая деятельность в 25 странах.
Задача
Компания приняла решение сократить простои на производственных линиях, чтобы более эффективно производить большее количество сортов пива. В рамках пилотного проекта на нескольких пивоварнях была поставлена задача сократить простои на 30% и затраты на 200 тыс. долл. Дополнительная цель – сокращение энергопотребления и повышение вовлеченности операторов.
Как использовался пакет Minitab
Для того чтобы выявить первопричину простоя, команда тщательно изучила значительный объем данных. Специалисты составили детальную схему производственного процесса и задокументировали отдельные потоки задач для каждого оператора. Они зафиксировали общий объем непродуктивных расходов, а также время, которое требовалось каждому рабочему на производственной линии на выполнение даже самых незначительных действий, таких как надевание перчаток и доступ к рабочим инструментам.
Они использовали широкий набор инструментов Minitab для того, чтобы проанализировать большой объем собранных данных, в том числе графиков Парето для того, чтобы определить факторы, сильнее всего влияющие на простои, гистограммы, необходимые для того, чтобы понимать функционирование процессов, а также контрольные карты и прочие графики для сравнения работы нескольких смен и пивоварен.
Также они использовали инструмент Minitab Assistant, который помогает выбрать правильный вид анализа и предоставляет максимально подробную отчетность для дисперсионного анализа и сравнения средних значений. Проверяя правдоподобие различных гипотез, специалисты выявили существенные различия в работе разных смен. Коробчатые диаграммы Minitab и другие графики рабочая группа использовала для того, чтобы визуализировать то, как различные смены меняли марки производимого пива.
В рамках анализа первопричин рабочая группа также использовала методику анализа Gage R&R, чтобы проанализировать работу измерительных систем и, перед тем как заниматься оптимизацией, убедиться в том, что их измерения достаточно надежны. По итогам анализа специалисты пришли к выводу, что показания циферблатных индикаторов могли быть ошибочными и данные по продолжительности процессов были ненадежными. Это проблему также необходимо было решить.
Благодаря внимательности специалистов к деталям и мощным инструментам анализа, предоставляемым Minitab, рабочая группа смогла определить основные причины чрезмерных простоев. Стандартная процедура по переоборудованию линии была далека от оптимальной. Кроме того, различные смены по-разному выполняли ее. Также они обнаружили, что аналогичные проблемы имелись и с другими процессами на других площадках.
В окончательный список решений вошли оптимизация процесса переоборудования посредством упорядочения и автоматизации задач, а также сокращение текущей громоздкой 30-страничной инструкции до 1-страничного чеклиста. Также была составлена программа тренингов для операторов производственной линии, а также добавлен напольный LED-таймер, чтобы информировать о точной длительности простоя и подчеркнуть необходимость срочных действий.
Для валидации этих решений рабочая группа разработала процедуру пилотного внедрения на небольшом участке, а также спрогнозировала эффективность решений для достижения исходных целей.
Результаты
Уже при пилотном внедрении улучшенных процедур результаты превзошли ожидания. Плановые простои сократились на 34%, сопутствующие расходы уменьшились более чем на $430 тыс. Благодаря сокращению простоев снизилось и энергопотребление, что также способствовало уменьшению затрат. Время на возобновление производства сократилось почти на 40%. Контрольные карты Minitab подтвердили наличие позитивных изменений.
На основе предложенных рабочей группой изменений было несложно создать набор рекомендаций, которые можно применять на других объектах и в других процессах. Операторы охотно начали использовать чеклист и выполнять другие действия, экономящие их время. Эффективность набора рекомендаций они оценили на 4,85 балла из 5. Получив эти результаты, проектная группа могла быть уверена в том, что набор рекомендаций можно эффективно применять в крупном масштабе. Именно так они и поступили: разработанный набор рекомендаций стали использовать для десятков тысяч процессов на более чем 180 объектах во всем мире.
Анализ данных о простоях на производстве с помощью Minitab принес непосредственную пользу компании Anheuser-Busch InBev и оказал долгосрочное положительное влияние на производственный процесс.
Планирование и оптимизация производства на предприятии. APS-система
Возможности для планирования производства
и повышения его эффективности
APS-cистема GoodsForecast.Scheduling берет на себя оптимизацию и моделирование производства посредством планирования расписания производственных смен. Модель, заложенная в основу работы APS-cистемы, учитывает следующие факторы:
- Производимый ассортимент и группы приоритетности.
- Ограничения по возможностям производства на каждой линии.
- Стоимость выключения и запуска производственных линий и стоимости их работы (свет, газ, вода).
- Плановое обслуживание производственных линий.
- Ограничения складов и стоимость отвлечения средств.
- Себестоимости и скорости производства товаров.
- Времена и стоимости переключений для каждой пары товаров (в том числе «разгон» линии и затраты на производство мембраны).
- Группы товаров по рецептуре, минимальные партии и кратности производства.
Решение для повышения эффективности
производства путем оптимизации
Оптимизация производственных процессов с помощью APS-системы GoodsForecast.Scheduling позволяет не только упростить мониторинг и анализ уровня запасов, но и производить планирование производства на предприятии с учетом прогноза спроса.
Прогноз
Учет годовой и недельной сезонности
Предобработка данных (дефицит, скачки продаж)
Промоакции и снижение цен
Экспертная корректировка пользователем
Уровень запаса
Оценка оптимального уровня запасов для обеспечения заданного уровня сервиса
Оценка оптимального уровня сервиса с учетом стоимости хранения товара и размера возможных штрафов
Расписание
Учет имеющихся заказов
Планирование производства продукции с учетом емкости склада и производственных мощностей
Оптимизация расписания на основе стоимости производства, стоимости переключений и штрафов
Преимущества внедрения APS-систем планирования
производства продукции на предприятии
- Значительное повышение эффективности работы завода или предприятия при помощи математических методов оптимизации расписания.
- Снижение влияния человеческого фактора, снижение количества ошибок.
- Формирование базы знаний процесса оперативного планирования, сокращение уровня зависимости работы завода от качества работы планировщика.
- Потенциальная централизация планирования производства на заводах компании.
Список модулей APS-системы для планирования
и оптимизации производства:
Базовый
Ядро
Оптимизация расписания работы производственных линий по известным заказам клиентов или в соответствии с планом, загружаемым в систему. Учет стоимости переключений, стоимости производства, штрафов за невыполнение планов (или заказов).
Дополнительный
Прогнозирование спроса
Среднесрочное прогнозирование спроса на готовую продукцию, учет прогнозируемых потребностей при планирование расписания работы линий.
Дополнительный
Учет сырья и материалов
Составление расписания производства с учетом фактического наличия и планов поставки сырья и материалов.
Дополнительный
Автоматический ответ на заявку клиента
Выставление оптимальных даты производства и даты отгрузки продукции для клиента.
История успеха
Корпорация «ТехноНИКОЛЬ» — крупнейший в России и Европе производитель и поставщик кровельных, гидроизоляционных и теплоизоляционных материалов. С целью сокращения издержек производства компании была внедрена APS-система автоматизации планирования производственных смен GoodsForecast.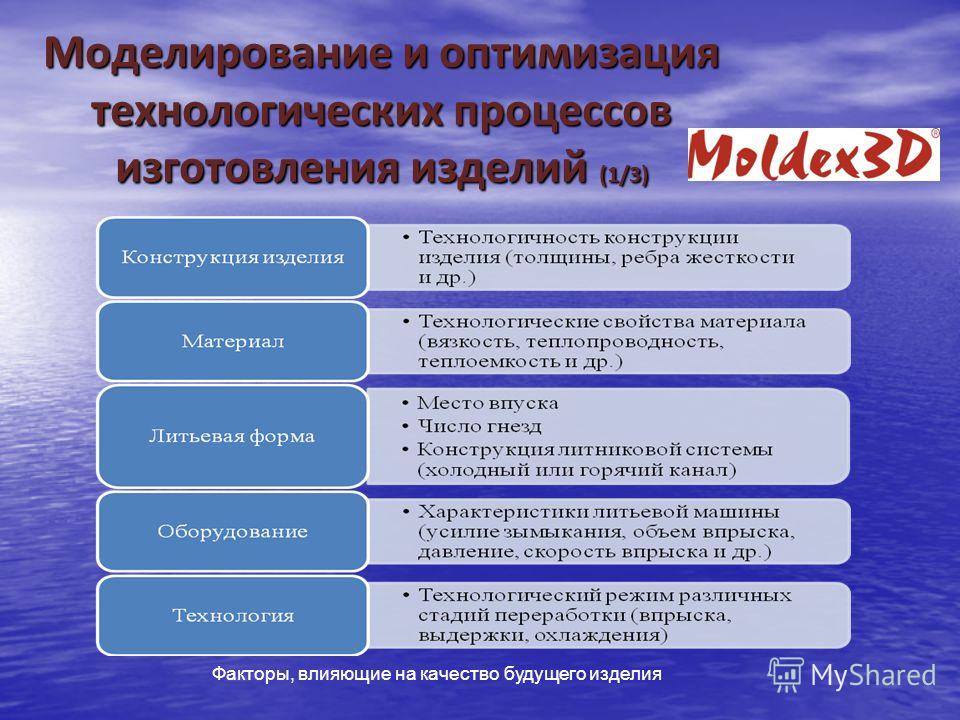
ВКР_Оптимизация производственного процесса с использованием инструментов бережливого производства (Оптимизация производственного процесса с использованием инструментов бережливого производства) — документ
Министерство транспорта Российской Федерации
Федеральное государственное бюджетное образовательное
учреждение высшего образования
«Дальневосточный государственный университет путей сообщения»
Институт экономики
Кафедра «Менеджмент»
К ЗАЩИТЕ ДОПУСТИТЬ
Заведующий кафедрой
____________ С.Н. Третьяк
«____» ___________ 2017 г.
ВЫПУСКНАЯ КВАЛИФИКАЦИОННАЯ РАБОТА
(БАКАЛАВРСКАЯ РАБОТА)
на тему: «ОПТИМИЗАЦИЯ ПРОИЗВОДСТВЕННОГО ПРОЦЕССА С ИСПОЛЬЗОВАНИЕМ ИНСТРУМЕНТОВ БЕРЕЖЛИВОГО ПРОИЗВОДСТВА»
ВКР (БР) 27.03.02 (134597)
Студент гр. 34А А.В. Баранова
Руководитель
к.э.н., доцент П.М. Сабитова
Нормоконтроль
к. э.н., доцент П.М. Сабитова
Хабаровск, 2017
РЕЦЕНЗИЯ
на выпускную квалификационную работу
студента группы 34А Барановой Арины Владимировны
Выпускная квалификационная работа Барановой А.В. посвящена вопросам использования модели бережливого производства в практической деятельности организации и выполнена в соответствии с заданной темой. Предоставленная на рецензирование выпускная квалификационная работа написана на основе деятельности хлебопекарни «ИП Самарина». В работе рассматриваются сущность и основные инструменты бережливого производства, анализируется производственный процесс организации. Текст сопровождается лаконичными выводами. Наглядно представлены сведения в удобной табличной и графической форме. Автор предложил свои рекомендации по оптимизации производственного процесса предприятия.
В целом в выпускной квалификационной работе обработан большой теоретический и собран практический материал. Студентка показала глубокие знания в данной области. Выпускная квалификационная работа написана профессиональным языком с достаточным привлечением необходимых документов и ссылок.
Выпускная квалификационная работа заслуживает оценку «отлично». Рекомендую присвоить выпускнику квалификацию: бакалавр в области управления качеством. Профиль подготовки: Управление качеством в социально-экономических системах.
Технолог
ИП «Самарина Л.П.» __________ _______________
АННОТАЦИЯ
Выпускная квалификационная работа разработана на тему «Оптимизация производственного процесса с использованием инструментов бережливого производства».
Выпускная квалификационная работа состоит из введения, отражающего актуальность выбранной темы и цель работы, трёх разделов и заключения, содержащего основные выводы и результаты анализа производственного процесса, и включает 86 страниц, 21 источника использованной литературы и 3 приложений.
1 раздел «Теоретические основы оптимизации бизнес-процессов» содержит систематизированные теоретические сведения и состоит из 22 страниц, одного рисунка и двух таблиц.
2 раздел «Общая характеристика деятельности и анализ производственного процесса на примере ИП «Самарина Л.П.» включает в себя общую характеристику деятельности хлебопекарни ИП «Самарина Л.П.», исследование системы качества и анализ производственного процесса предприятия. Раздел состоит из 23 страниц, 6 рисунков и 8 таблиц.
3 раздел «Проектные предложения по оптимизации производственного процесса ИП «Самарина Л.П.» путём внедрения инструментов бережливого производства» состоит из 11 страниц, 4 рисунков, 3 таблиц и одной формулы.
ABSTRACT
Thesis project was developed on the theme «Optimization of the production process using tools of Lean production».
Final qualifying work consists of introduction, reflecting the relevance of the chosen topic and aim of the work, three chapters and conclusion, contains the main conclusions and results of the analysis of the production process, and includes 86 pages 21 sources of literature and 3 application.
1 section «Theoretical bases of optimization of business processes» contains systematized theoretical information and consists of 22 pages, one figure and two tables.
2 section «General characteristics of activities and analysis of the production process by the example of an individual entrepreneur L.P. Samarina» includes a general description of the activity of the bakery individual entrepreneur L.P. Samarina, a study of the quality system and analysis of the production process of the enterprise. The section consists of 23 pages, 6 figures and 8 tables.
3 section «Project proposals for optimization of the production process of individual entrepreneur L.P. Samarina by introducing Lean production tools» consists of 11 pages, 4 figures, 3 tables and one mathematical formula.
СОДЕРЖАНИЕ
ВВЕДЕНИЕ 12
1 ТЕОРЕТИЧЕСКИЕ ОСНОВЫ ОПТИМИЗАЦИИ БИЗНЕС-ПРОЦЕССОВ 15
1.1Понятие и виды процессов в организации 15
1.2 Управление и оптимизация процессов в организации 21
1.3 Бережливое производство как инструмент оптимизации: сущность, основные инструменты 27
2 ОБЩАЯ ХАРАКТЕРИСТИКА ДЕЯТЕЛЬНОСТИ И АНАЛИЗ ПРОИЗВОДСТВЕННОГО ПРОЦЕССА НА ПРИМЕРЕ
ИП «САМАРИНА Л. П.» 37
2.1 Общая характеристика организации 37
2.2 Анализ внешней и внутренней среды организации 39
2.3 Исследование организационной структуры и структуры персонала 43
2.4 Исследование системы менеджмента качества организации 47
2.5 Анализ качества производственного процесса 54
3 ПРОЕКТНЫЕ ПРЕДЛОЖЕНИЯ ПО ОПТИМИЗАЦИИ ПРОИЗВОДСТВЕННОГО ПРОЦЕССА ИП «САМАРИНА Л.П.» ПУТЁМ ВНЕДРЕНИЯ ИНСТРУМЕНТОВ БЕРЕЖЛИВОГО ПРОИЗВОДСТВА 59
3.1 Обоснование необходимости внедрения инструментов в деятельность организации 59
3.2 Описание алгоритма и расчёт эффективности внедрения инструментов бережливого производства 63
ЗАКЛЮЧЕНИЕ 74
СПИСОК ИСПОЛЬЗОВАННЫХ ИСТОЧНИКОВ 78
ПРИЛОЖЕНИЕ А 81
ПРИЛОЖЕНИЕ Б 85
ПРИЛОЖЕНИЕ В 86
ВВЕДЕНИЕ
Производственный процесс – это деятельность по преобразованию входных ресурсов в определённый тип продукции, в основе которой лежит труд. Основной частью производственного процесса являются технологические процессы, которые содержат целенаправленное воздействие по изменению и определению состояния предметов труда. В ходе реализации технологических процессов происходит изменение геометрических форм, размеров и физико-химических свойств предметов труда.
Наряду с технологическими производственный процесс включает также и нетехнологические процессы, к которым относятся транспортные, складские, погрузочно-разгрузочные, комплектовочные и некоторые другие операции и процессы.
Совершенствование производственных процессов – это очень широкая тема, допускающая множество подходов. В общем виде основные усилия по совершенствованию производства всегда направлены в следующих направлениях:
управление производственной мощностью;
управление запасами;
непрерывное совершенствование;
управление цепью поставок и снабжения;
наращивание производственных возможностей.
Обычно оптимизация производственных процессов ставит перед собой две цели: повышение эффективности производства в целом и сокращение затрат. Как правило, конечная цель достигается за счет внедрения более современных технологий и улучшения организации труда. Здесь на помощь приходит концепция бережливого производства, позволяющая с помощью некоторых простых инструментов и минимума затрат перестроить деятельность в сторону большей эффективности процессов.
Актуальность темы, выбранной для дипломного проектирования, обусловлена тем, что концепция бережливого производства прекрасно зарекомендовала во всех сферах производства, а значит, для достижения устойчивого успеха организации необходимо «держать руку на пульсе» и оперативно подстраивать свою деятельность под те условия, которые диктует рынок. Эффективно осуществлять такую деятельность помогают инструменты бережливого производства, которые достаточно легко встраиваются в практически любой процесс.
Объект исследования – хлебопекарня ИП «Самарина Л.П.».
Предметом исследования выпускной квалификационной работы является производственный процесс хлебопекарни ИП «Самарина Л.П.».
Цель выпускной квалификационной работы – разработка предложений по оптимизации производственного процесса с использованием инструментов бережливого производства.
Данная цель предполагает постановку и решение следующих задач:
исследовать теоретические аспекты оптимизации процессов организации;
рассмотреть понятие бережливого производства и дать характеристику инструментов, применяемых в этой концепции;
проанализировать деятельность хлебопекарни ИП «Самарина Л.П.»;
на основе проведённого анализа обосновать целесообразность внедрения инструментов бережливого производства в деятельность исследуемой организации;
предложить алгоритм внедрения инструментов и произвести расчёт экономической эффективности предлагаемых мероприятий.
Для достижения исследовательской цели и решения поставленных задач использован комплекс научных методов, включающий в себя анализ литературных источников, наблюдение за производственными процессами организации, анализ внутренней документации предприятия, анализ полученных результатов.
Основными литературными источниками, послужившими опорой при написании теоретической части работы послужили труды таких авторов, как В. А. Гагарский, Н.С. Давыдова, И.В. Еманаков, Дж. П. Вумек, Т. Фабрицио и другие.
Выпускная квалификационная работа состоит из введения, трёх разделов, заключения, списка используемых источников и приложений.
Во введении раскрывается актуальность выбранной темы, ставятся цели и задачи работы, определяется объект и предмет исследования.
В первом разделе раскрываются теоретические основы оптимизации бизнес-процессов и даётся краткая характеристика концепции бережливого производства и основных инструментов, применяемых при реализации этого подхода в деятельности предприятий.
Во втором разделе выпускной квалификационной работы приводится характеристика исследуемой организации, в том числе характеристика персонала, организационной структуры и системы качества на предприятии, а так же приведена технологическая схемы основного производственного процесса – выпечки хлеба. На основе анализа деятельности хлебопекарни были
В третьем разделе на основе проведённого анализа объекта исследования и исследования теоретических разработок по данной теме были предложены алгоритмы внедрения некоторых инструментов в производственный процесс организации и дано обоснование их целесообразности с расчётом экономической эффективности.
В заключении сделаны ключевые выводы про всем разделам выпускной квалификационной работы.
1 ТЕОРЕТИЧЕСКИЕ ОСНОВЫ ОПТИМИЗАЦИИ БИЗНЕС-ПРОЦЕССОВ
Понятие и виды процессов в организации
Любой процесс в организации – прежде всего определенная совокупность действий, направленных на преобразование входящих ресурсов в выходной результат (продукцию, услугу и т.д.). Отсутствие вообще каких-либо процессов в организации означает, что предприятие не функционирует.
В любой организации, в зависимости от её масштаба и формы деятельности, одновременно протекает большое число процессов, различающихся не только по целевому назначению, но и по основным характеристикам. Существует множество различных подходов к классификации процессов. При самом общем и простейшем подходе все процессы делят на материально-вещественные и информационные. Оба типа процессов, так или иначе, присутствуют на любом предприятии, но в зависимости от вида деятельности один из них является превалирующим (например, на предприятиях пищевой промышленности доминирующими являются процессы, носящие материально-вещественный характер).
Исследование эффективности организации процессов на предприятиях следует вести через категорию бизнес-процесса [7]. Однако, стоит отметить, что не существует устоявшегося определения бизнес-процесса. Встречающаяся в литературе терминология, чаще объясняется заимствованием из английского языка. В настоящее время существует множество определений понятия «бизнес-процесс». Все они описывают бизнес процесс с различных точек зрения.
Андерсен Бьёрн дает следующее определение элементу процесс [12]: «… некоторая логическая последовательность, связанных действий, которые преобразуют вход в результаты или выход»
Используя определение Эрикссона можно сказать следующее [7]: «Бизнес-процесс — это: цепь логически связанных, повторяющихся действий, в результате которых используются ресурсы предприятия для переработки объекта (физически и виртуально) с целью достижения определенных результатов или продукции для удовлетворения внутренних и внешних потребителей».
Рассмотрим данное определение более подробно. Итак, важной частью любого бизнес-процесса является потребитель. Потребитель может быть, как внешним, так и внутренним по отношению к организации. Внешний потребитель — это потребитель, который не входит в состав данной организации, а внутренний — тот потребитель, который находится в рамках данной организации.
Важно знать потребителя бизнес-процесса потому, что именно он явным или неявным образом задает требования к процессу и может оказывать влияние даже на сам факт существования конкретного процесса.
Другой частью понятия бизнес-процесс является результат. Результат бизнес-процесса — это наиболее важная его составляющая. Деятельности без результата не бывает; иначе это не деятельность, а бесцельное времяпрепровождение. Без достижения результата (причем с требуемыми потребителю характеристиками) деятельность бессмысленна. А от того, как процесс выстроен, зависят в том числе и издержки этого процесса.
У бизнес-процесса должен быть единый менеджер, который управляет процессом и отвечает за его результат. На практике часто бывает (это характерно для крупных компаний), что у бизнес-процесса есть так называемые владелец и менеджер процесса. Обе эти фигуры отвечают за результаты, но при этом владелец процесса обладает полномочиями изменять сам порядок выполнения процесса, а менеджер процесса осуществляет оперативное управление.
Оптимизация производственных процессов | Рус-ЭКС
Оптимизация — это процесс нахождения наилучших (оптимальных) решений различных (производственных, бизнес-задач и т.д.) задач с использованием математических моделей. Задачей (проблемой) оптимизации является минимизация или максимизация каких-либо необходимых показателей в процессе организации производства и принятия решений, таких как общее затраченное время, фактическая продолжительность, стоимость и т.д., учитывая заданные условиями реальной задачи ограничения.
Проблемы оптимизации возникают во всех областях производства и экономики, например, разработка технологического процесса, увеличение производительности, логистике, управлении трафиком, транспортными потоками, рабочей нагрузкой, стратегическом планировании и т.д. В первую очередь необходимо создать математическую модель реальной задачи. Математическая модель реальной системы — это совокупность математических соотношений (такие как уравнения, неравенства, логические условия), которая является обобщением рассматриваемой реальной задачи. Обычно математическая оптимизационная модель состоит из четырёх ключевых объектов: исходных данных, неизвестных, ограничений и целевой функции. Исходные данные представляют требования задачи. Это могут быть стоимости или потребности в ресурсах, условия эксплуатации оборудования, вместимость складов, грузоподъёмность транспорта и т.д. Переменные представляют Ваше решение: Сколько определённой продукции необходимо производить, открывать новую линию обслуживания или нет, сколько и какие запасы держать на складе. Ограничения могут быть самыми различными: количественные соотношения, ограничения по объёму, вместимости и т.д. Целевая функция представляет желаемое направление оптимизации: минимизация цены, максимизация коэффициента использования, минимизация затрат и т.д.
Наиболее применимы оптимизационные методы для решения производственных и бизнес-задач по следующим направлениям: планирование производства, планирование работ и календарное планирование, моделирование распределения ресурсов, движение товаров и логистика, оптимизация нефтеперерабатывающей и нефтехимической промышленности, планирование технологических процессов, техническое проектирование, планирование вложения капитала, сетевое планирование, финансовая оптимизация. Построение эффективного производства невозможно без определения цели оптимизации. Для промышленных предприятий целью любых производимых изменений является увеличение дохода от производственной деятельности. Это возможно при одновременной оптимизации основных параметров производства: оборота, операционных расходов, запасов. Необходимо определить, как влияет изменение данных параметров на производство.
В данном случае рассмотрим увеличение оборота, которое можно осуществить путем увеличения объемов продаж либо увеличением цен. Исходя из рыночной ситуации и покупательной способности, понимаем, что цены на производимые товары уже максимальны, а дальнейшее их увеличение без тенденции роста у конкурентов приведёт к уменьшению спроса на товар. Увеличение объема продаж возможно за счет: снижения цены (себестоимости товара), вывода на рынок новой продукции (быстрее, чем конкуренты), предоставления более качественных товаров и услуг, быстрого предоставление товаров и услуг потребителю (быстрее, чем конкуренты). Снижение цены за счет себестоимости тоже имеет свои пределы, маржу снижать до бесконечности невозможно, либо она и так уже минимальна. Предоставление более качественных товаров и услуг так же не будем рассматривать, потому что резонно считать, что все предприятия уделяют этому показателю примерно равное внимание. Быстрое предоставление товаров и услуг потребителю (быстрее, чем конкуренты) – при равной цене, равном качестве, равных условиях поставки выигрывает тот, кто быстрее доставит потребителю товар или услугу. Очевидно, что операционные расходы необходимо сокращать. В общих случаях это можно осуществить, если: снизить численность, повысить эффективность работы персонала, уменьшить складские и производственные помещения. Практика показывает, что административно-управленческое снижение численности персонала не приводит к одновременному повышению эффективности работы предприятия, а напротив приведет к уменьшению объема производства и потере качества. Повышение эффективности работы персонала реализуется за счет снижения трудоемкости выполнения операций, процедур (как производственных, так и технических, организационно-управленческих). Для примера рассмотрим следующую ситуацию: мастеру поставлена задача выпустить за рабочую смену на станке четыре партии изделий по две штуки (четыре разных номенклатуры предметов производства) для сдачи двух комплектов (или двух изделий) заказчику. Для того, чтобы все сделать в одну смену необходимо переналаживать станок четыре раза. Итого восемь штук = восемь нормо-часов. Это «условные» т.е. «зарплатные» нормо-часы. Следует обратить внимание, что на предприятии действует сдельная оплата труда. Если делать по одной партии в день, соответственно переналаживать станок один раз в день (в смену) можно сделать по двадцать штук каждого наименования предмета производства, и получить за каждый день по двадцать условных нормо-часов. В результате, номенклатура в задании есть, заготовки есть, товарная трудоемкость цеха выше. Какой же вариант выберет мастер? Скорее всего, второй. Ведь второй вариант – это более высокая зарплата, более высокий показатель загрузки оборудования, более высокая локальная эффективность. И это стандартная ситуация, ежедневно наблюдаемая на производстве. Стандартная она не потому, что правильная, а потому что по такой схеме работают большинство Российских предприятий. Резюмируя, с точки зрения эффективности производственной системы в целом: потратили материалы на 20 комплектов вместо 2, заплатили зарплату за изготовление 20 комплектов вместо 2; и может быть когда-нибудь в перспективе эти комплекты, и пригодятся. А может быть и нет, заказа такого не будет, конструкция поменяется. Кроме того в результате работа выполнялась четыре дня вместо одного. Вот реальная «эффективность» нашего производства, не говоря уже о клиенте, который ждет. Рассмотрим, какие могут быть варианты решения. Первый вариант — переход на повременную оплату. В этой ситуации «плюс» в том, что мастеру все равно что и сколько делать, «минус» – все равно делать ли что-либо вообще. Второй вариант — оплата за сдачу товарной продукции только в объеме существующего заказа на текущий месяц. Следует заметить, что генеральный директор одного из предприятий так и поступил. Если за текущую неделю сдавался 100% объем потребности текущего месяца, то к ФОТ цеха за эту неделю добавляли 50%, если такая ситуация была все недели в течение текущего месяца, то плюс еще 50% премии к ФОТ цеха, т.е. цех может суммарно получить 200% ФОТ. Это в целом для предприятия оказалось выгоднее, т.к. весь персонал на 100% был заинтересован производить только то, что нужно для заказчика. Ускорение времени выполнения заказа увеличилось почти в два раза. Однако по прежнему не была решена проблема ускорения операционного времени. Вариант 3: SMED – один из инструментов Бережливого производства. «Плюс» – снижение времени изготовления комплекта, «минус» – отсутствие мотивации к снижению времени, выполнению именно заданной номенклатуры, а не какой-либо другой. Как же поступить в этой ситуации и какой вариант решения выбрать? Правильный ответ — совокупность всех трех вариантов. Именно в этом случае произойдет повышение эффективности производственного процесса. Вместо целого дня работы мастер будет работать не более 4 часов, и, главное, он будет нацелен на достижение общей цели предприятия. Снижение объема производства не рассматриваем в виду его нецелесообразности. Более быстрый «оборот» материалов, более быстрые производственные циклы при неизменных объемах производства приведут к высвобождению производственных, складских площадей, что равнозначно созданию резерва ресурсов для увеличения объема производства. Административное снижение запасов производства приведет к снижению планового задела производства, что в свою очередь негативно скажется на эффективности производства в целом. Простое (без разработки соответствующих механизмов снижения) введение показателей «уровень НЗП», «уровень ТМЦ», никогда не приведет к одновременному повышению эффективности. Например, на одном из предприятий при внедрении информационной системы (ERP-системы) большое внимание уделялось снижению запасов. Результат внедрения — учитывая тот факт, что система была настроена на оптимизацию запасов и работала исправно, ровно через два месяца работа в сборочном цехе остановилась. Для информации: предприятие ранее работало действительно с реально высоким уровнем запасов, информационная система была внедрена правильно (в части расчета норм расхода и определения потребности), нормы расхода материала заведены правильно и в полном объеме. Тип производства – проектное, под заказ. Достаточно низкий уровень сдачи «с первого предъявления», длительные циклы производства, сборки, частые, долго внедряемые конструкторские изменения, случались срывы поставок материалов и ПКИ. Так почему же остановилась работа? Высокий уровень заделов «покрывал» низкое качество производства, длительные процедуры изменений (при конструкторских изменениях), срывы поставок. Ни одна из этих причин при внедрении не была решена. Отсюда вывод: высокий уровень запасов – это не причина, а следствие. Снижать его административно, не изменив причин, приведших к его образованию больше похоже на лечение кашля вместо ангины. Решение в иной системе оценки состояния запасов: Более «правильный», «честный показатель» — время нахождения запасов в производственной (складской) единице. На одном из предприятий была разработана система оценки времени нахождения запасов в производственных, складских подразделениях и введены показатели «залежалые запасы НЗП», «залежалые запасы ТМЦ». Система сигнализировала руководству не о превышении некого «общего уровня материалов и заделов», а о превышении времени нахождения материалов в цехах и на складах, что позволило создать наглядную картину «динамического определения узких мест всех производственных подразделений в реальном времени». Снижение объема производства – не желательно, а вот более быстрый оборот материалов, через сокращение общего времени производственного цикла решает проблему снижения общего уровня запасов в производстве. Очевидно, что есть только один параметр на который непосредственно можно влиять и который не зависит от других — время. Изменение этого параметра влечет за собой изменение всех остальных. Время операционное, выполнения процедур, реакции на изменения. Сократив операционное время, мы увеличим производительность. Чем быстрее предприятие адекватно реагирует на изменения в производственной системе, чем быстрее появляется возможность правильно скорректировать план производства, тем эффективнее оно работает. Однако следует помнить, что неадекватная реакция руководства на производимые в подразделениях улучшения способна остановить любые изменения. Или, на предприятии было объявлено о проекте повышения эффективности освоения новых изделий. В работах по освоению изделия задействовано много подразделений: отделы главного конструктора, отдел главного технолога, инструментальное производство и т.д. Все, кроме одного «отделались» формальными отчетами и не провели никаких изменений. Одно из подразделений «поддалось» на проведение изменений, были оптимизированы внутренние процессы, скорость прохождения работ резко увеличилась. Так как общая эффективность производства работ не выросла, то при очередной волне сокращений в попытке хоть как-то сократить издержки были сокращены сотрудники именно данного подразделения, так как все остальные были заняты на 100% и при этом ничего не успевали. Их сократить означало остановить деятельность всего предприятия. Можно представить какой удар получили люди, реально повысившие свою производительность. Про дальнейшие попытки повышения эффективности процессов можно забыть на долгие годы.
Тотальная оптимизация производства – проект, направленный на повышение эффективности производства «снизу-вверх», т.е. на предприятии создается управленческий механизм, который позволяет выдвигать, оценивать и реализовывать рационализаторские предложения «снизу», минуя административные препоны. Возможные направления программы: сокращение затрат, повышение надежности поставок, повышение качества (брак и время простоев), утилизация отходов, устранение «узких мест» в производстве.
На первом этапе проекта определяются цеха или участки, в которых будет реализовываться проект, создается проектная структура, состоящая из рабочих групп на уровне производственных отделов и цехов, а также управляющего совета, который принимает решения по внедрению того или иного улучшения. Также производится анализ затрат: они разделяются на сокращаемые и не сокращаемые. На основе анализа затрат определяются цели по их сокращению. Так как рационализаторские предложения, по сути, являются внутренними инвестиционными проектами, то для них устанавливаются критерии с точки зрения эффективности, максимального срока окупаемости и размера инвестиций.
После завершения подготовительной стадии проекта рабочие группы в режиме «мозгового штурма» анализируют пути оптимизации деятельности своих производственных единиц, генерируют идеи и отбирают наиболее реалистичные. Затем предложения оформляются в виде проектов. Оценивается сумма необходимых инвестиций, рассчитывается экономический эффект от внедрения, подготавливается предварительный план внедрения. Далее, предложения выносятся на управляющий совет, который принимает или отвергает тот или иной проект. Во время реализации проекта управляющий совет или специально выделенная группа внутренних контролеров осуществляют мониторинг хода внедрения, расходования выделенных средств и графика выполнения работ. Окончательную оценку результативности рацпредложения можно сделать на основании анализа эффекта, который оно принесло, например, путем анализа соответствующих показателей в системе управленческого учета затрат до и после внедрения. Реализацию программы тотальной оптимизации производства можно разбить на две фазы. Первая – когда на предприятии создаются необходимые управленческие механизмы, в результате начальных мозговых штурмов находятся существенные резервы сокращения затрат и внедряются соответствующие улучшения. Второй этап – когда программа начинает работать на постоянной основе.
Для успешной реализации проекта ТОП необходимо придерживаться следующих принципов:
1. Никто лучше сотрудников предприятия не разбирается в собственном производстве, а значит, не может определить направления повышения его эффективности. Работа внешних консультантов при этом заключается в стартовом направлении инновационного процесса, формировании и передаче методологии анализа затрат и материальных потоков, организации процесса (функции и порядок взаимодействия внутри предприятия), а также в выполнении сопутствующих работ, обеспечивающих успешную реализацию проекта ТОП (например, разработка механизмов дополнительной мотивации персонала).
2. При обсуждении проектов на рабочих группах следует рассматривать даже самые смелые и фантастические идеи.
3. За принятые и реализованные рацпредложения сотрудники должны быть вознаграждены материально, что будет служить значительной мотивацией персоналу, участвующему в проекте.
4. Программа по оптимизации должна поддерживаться высшим руководством предприятия и находиться под его постоянным контролем.
В заключение стоит отметить, что оба подхода – бережливое производство и тотальная оптимизация производства основываются на раскрытии творческого потенциала сотрудников предприятия. В отличие от других управленческих технологий, ориентированных на жесткую регламентацию деятельности и усиление контроля «сверху-вниз», данные подходы позволяют вовлечь в процесс оптимизации работников всех уровней. При этом достигается комплексный эффект: предприятие работает более эффективно, сотрудники вовлечены в процесс реализации проекта и имеют возможность улучшить свои условия труда и материальную компенсацию.
Факторы успеха проекта на практике
1. Ориентировать всех участников создания стоимости на согласованную общую долгосрочную цель — идеальное состояние потока стоимости. При этом разбить поток на определенные этапы, его целевые состояния. Компания должна сделать этот шаг для приближения к идеальному состоянию. При этом неясно, как это новое состояние должно и может быть достигнуто. Результат определен заранее, а путь его достижения открыт для творчества.
2. Разложить поток создания стоимости на отдельные управляемые людьми или командой организационные единицы (сегменты, участки). Такой подход создает возможность контролировать отдельные процессы и влиять на них. Если этого не сделать и рассматривать все производственные процессы как единый поток с его взаимосвязями, система будет неуправляемой, поскольку образуются функциональные бункеры, связанные между собой только потоками материалов и информации.
3. Для выполнения задачи менеджмента — организации процесса систематического достижения поставленной цели — использовать следующий алгоритм: определить параметры состояния потока стоимости в качестве целевого ориентира в направлении заданной идеальной цели, выделенные сегменты или участки в общем потоке создания стоимости должны быть в состоянии, независимо от проблем в других участках, выполнить свою роль и достичь поставленной цели. А чтобы изменения в одном сегменте напрямую не влияли на другой и не были решающей причиной недостижения целей, отдельные сегменты соединяют между собой через буфер. Взаимные влияния можно нивелировать, например, через запасы (супермаркеты с установленными мини- и макси-запасами), мощности (стандартные и дополнительные мощности, используемые при появлении узких мест) или время. При этом распределение по сменам и плановая загрузка каждой смены составляет только 70% при обязательном выполнении всех запланированных заказов. Только в этом случае можно устанавливать цели для каждого сегмента как стандарт, который независимо от проблем в другом должен быть достигнут. Если же это не удается, необходимо выявлять причины и устранять их.
4. Для достижения долгосрочного процесса улучшений вначале опытным путем на практике определить, возможно ли достижение оперативной цели регулярно. И лучше всего сделать это без применения ИТ. Работники должны отмечать каждый час, какие номера деталей они обработали, их количество в час и какой был план. При отклонении факта от плана работники записывают причины недостижения результата. Затем причины группируются по частоте их возникновения, и проводится анализ по принципу Паретто. Отдельные причины отрабатываются отдельно и представляется их результат. Такой систематический цикл решения проблем очень важен для получения устойчивых улучшений результатов оперативного процесса
Систематизируя, решение на уровне топ-менеджмента о необходимости усовершенствования производственной деятельности на предприятии состоит из: привлечения внешних специалистов, отбора инициативной группы и обучение этой группы, набора и отбора идей, их анализа, разработка программы оптимизации производства, выделение финансирования, реализации программы оптимизации производства, контроля внедрения этой программы, анализа результатов проведенной работы, работой над затратами, которые можно оптимизировать, контроль над ненужными операциями, совершенствование производственных приемов.
Оптимизация бизнес-процессов промышленного предприятия на основе внедрения процессного подхода
1197
креативная экономика № 11’2017 (ноябрь)
ОБ АВТОРАх:
Бабикова Анна Валерьевна, кандидат экономических наук, доцент, доцент кафедры экономики
предприятия (а[email protected])
Корсаков Михаил Николаевич,кандидат экономических наук, доцент, профессор кафедры экономики
предприятия ([email protected])
Сарафанов Андрей Дмитриевич, инженер по организации и нормированию труда, ЗАО Творческо-
производственное объединение «Лемакс», Таганрог, Россия ([email protected])
ЦИТИРОВАТЬ СТАТЬЮ:
Бабикова А.В., Корсаков М.Н., Сарафанов А.Д. Оптимизация бизнес-процессов промышленного
предприятия на основе внедрения процессного подхода // Креативная экономика. – 2017. – Том 11. –
№11. – С.1195-1208. doi:10.18334/ce.11.11.38474
ясное понимание того, как функционирует организация, позволяет увидеть и свести
к минимуму процессы, не создающие ценности для потребителя, а значит, сократить
свои издержки и получить конкурентное преимущество на рынке [3] (Ishmuradova,
Shagaipov, 2016).
Особенности процессного подхода в управлении предприятиями и организаци-
ями в достаточной степени представлены в отечественной и зарубежной литературе
[4-6] (Komissarova, 2011; Medvedev, 2016; Ostroukhova N.G., 2015). Широко известна
работа М. Хаммера и Дж. Чампи «Реинжиниринг корпорации. Манифест революции
в бизнесе», в которой описана методология реижиниринга, рассмотрен опыт ведущих
компаний по организационной перестройке бизнеса [7] (Khammer, Champi, 1997).
М.Хаммер и Дж. Чампи предлагают инструментарий, гарантирующий существенную
экономию производственных и временных затрат, формирующий компанию нового
типа, ориентированную на достижение высоких конкурентных позиций.
Несмотря на многообразие подходов к процессу управления промышленными
предприятиями, разработке и внедрению процессного подхода в практику их деятель-
ности, остается ряд актуальных вопросов, связанных с необходимостью формирова-
ния технологий, методов и механизмов оптимизации бизнес-процессов предприятия.
Выделение, описание и управление бизнес-процессами организации, согласно концеп-
ции реинжиниринга, реализует управленческую методологию, позволяющую сущест-
венно повысить эффективность хозяйственной деятельности в целом. Традиционно
реинжиниринг предприятия рекомендуется проводить с целью полной перестройки
деятельности предприятия в случае угрозы банкротства, перепроектирования биз-
нес-процессов в системе антикризисных мер и для совершенствования процессного
управления успешного предприятия с целью повышения устойчивости и конкурен-
тоспособности [8] (Petukhov, 2013). В данной работе предлагается использовать мето-
дики реинжиниринга для оптимизации производственной деятельности предприятия
на основе экономико-математического моделирования с использованием регрессион-
ного анализа.
Отчет о проделанной работе. Оптимизация производственных процессов
1. Отчет за период с 01.01.15 по 31.12.15 по проекту оптимизации производственных процессов.
2. Работа в Столярном цеху
1) Завершена переработка РМ сборщиков столов в столярном цеху. Введен в эксплуатацию стол свращающейся столешницей, который был предложен в качестве рац. предложения сборщиком Соколюком
С.Ю. Внедрение данного стола позволило ускорить сборку шпонированных и пластиковых столов
примерно на 8%, а применение пневматического инструмента с регулировкой силы затяжки позволило
сделать выполнение операций по вкручиванию саморезов более простым и удобным.
2) Разработана и установлена «Доска предложений» для получения обратной связи от работников цехов, в
том числе и столярного. По задумке, данный инструмент был призван упростить коммуникацию с
рабочим персоналом и призвать их к более активному предложению рационализаторских идей. По ряду
причин, широкой популярности данная методика не получила.
3) Переработаны и переоснащены рабочие места карусельно-фрезерного станка (Сидоров К.), группы
ручных фрезерных станков (Мякишев К.) и группы шипорезных станков Balestrini (Сиразев Р.). В
результате переоснащения была решена проблема нехватки ручного инструмента на данных рабочих
местах, у каждого оператора появился собственный набор ручного инструмента, приспособленный для
решения задач именно на его рабочем месте. Для каждого РМ были изготовлены шкафы для хранения
ручного инструмента.
4) Организация пересылки вальцов клеемаза в Петербург для их восстановления. Курирование процесса
поставки вальцов обратно на фабрику.
3. Работа в Столярном цеху
5) Проведен эксперимент с использованием инструментальных подсумков. Эксперимент показал, что такиеподсумки могут быть полезны лишь в случае постоянного перемещения рабочего от одного станка к
другому. Данная сумка может пригодиться руководящему персоналу цехов для переноски измерительных
инструментов и некоторых канцелярских принадлежностей.
6) Нанесена разметка на полу столярного цеха для обозначения мест стоянки тележек с полуфабрикатами и
их движения по цеху. Разметка наносилась с помощью скотча трех цветов: красный, желтый и зеленый.
Красный цвет разметки означает запрет на пересечение и остановку тележек. Желтый цвет означает
парковочные места где нужно ставить тележки. Зеленая разметка обозначает проходы, которые должны быть
свободны для перемещения телег, поддонов и персонала. Данная разметка позволила частично улучшить
координацию в столярном цеху.
7) Изготовлены и установлены на тележки прозрачные кармашки для хранения бирок. Как результат,
движение полуфабрикатов продукции внутри цеха стало намного прозрачнее. Каждая бирка на телеге
содержит всю необходимую информацию о продукции, которая на ней находится. Владея такой
информацией намного легче отследить движение продукции в потоке.
8) Переработана кладовая столярного цеха. Изготовлены и установлены новые полки для хранения лотков с
метизами, мебельных комплектующих. Проведена подборка и установка пластиковых лотков в соответствии
с размерами мебельных комплектующих.
4. Работа в Цеху корпусной мебели
1) Введены в работу инструкции по уборке и обслуживанию станков корпусного цеха. Каждый станокимеет индивидуальную наглядную цветную инструкцию с указанием и описанием операций по
уборке. Каждый станок подкреплен журналом учета ведения уборки, который проверяет мастер цеха
и главный инженер предприятия.
2) Разработаны и введены в эксплуатацию рабочие столы для сборщиков корпусной мебели. Данные
столы сделали их работу более удобной, создали места для хранения метизов и мебельных
комплектующих, сократили количество брака из-за царапин на поверхностях столов.
3) Переработан индивидуальный набор ручного инструмента сборщиков корпусной мебели. Закуплен и
введен в эксплуатацию инструмент, необходимый для сборки корпусной мебели (молотки, киянки,
плоскогубцы и т.д.)
4) Разработка и установка металлического стеллажа для хранения бухт с кромкой. Как результат –
экономия пространства для хранения материала и создание упорядоченности расположения бухт (по
цвету, ширине, толщине).
5. Работа в Цеху мягкой мебели
1) Разработка и введение в эксплуатацию устройства по отмотке нитей для утяжки диванов Калинка всоответствии с рационализаторским предложением обойщика Макарова А.
2) Подбор, закупка и установка стеллажей для хранения метизов и мебельных комплектующих для склада
цеха мягкой мебели. Заполнение стеллажей лотками соответствующих размеров, назначение мест
хранения метизов и комплектующих.
3) Разработка, нанесение и введение в эксплуатацию линеек измерительных на рабочих местах швей и
раскройщиков. Ремонт стола раскройки материала. Измерительные линейки были так же нанесены в
столярном цеху и матрасном цеху.
6. Работа в Административном корпусе
1) Внедрение в работу офисных работников CRM-системы «Мегаплан». Проведение разъяснительных работс персоналом о принципе работы системы и ее необходимости. Поддержание системы на
работоспособном уровне и внесение сотрудников офиса в систему.
2) Разработка плана помещения столовой и подбор кондиционера для установки в столовой. Курирование
процесса поставки и установки кондиционера.
Что такое оптимизация производства? | TIBCO Software
Методы оптимизации производства
После создания основы для оптимизации производства предприятия могут использовать следующие методы для реализации оптимизации:
Прогноз ожиданий рынка
Каждое производственное предприятие должно оценить необходимые объемы производства. К сожалению, у большинства организаций нет оценок будущих продаж. Продажи можно прогнозировать, изучая исторические данные о продажах и преобладающие рыночные тенденции.Имея передовые инструменты отчетности, организация может получить точную информацию о продажах и запасах компании.
Управление запасами
Ключевым инструментом планирования и оптимизации производства является процесс управления запасами качества. Этот процесс сложно выполнить вручную, и его следует автоматизировать. Автоматизация системы управления запасами поможет компании в любое время увидеть, какие ресурсы у нее есть под рукой. С помощью качественной системы управления запасами специалисты по планированию производства могут отслеживать уровни запасов и автоматизировать их пополнение.Автоматизированные системы могут даже прогнозировать потребности в запасах.
Подготовить персонал к производству
Компании должны быть уверены, что оборудование и рабочая сила доступны в любое время. Для хорошей оптимизации производства важно оценить, сколько сотрудников необходимо для производственного процесса и какой должна быть их компетенция. Очень важно обеспечить сотрудников необходимыми инструментами и пройти необходимое обучение работе с передовым оборудованием.
Стандартизация шагов и управления временем
Каждый производственный процесс должен знать, где и когда происходит каждый этап и сколько времени требуется для его завершения.Имейте в виду, что не все этапы происходят последовательно — некоторые происходят в тандеме, а некоторые следуют установленной последовательности. После того, как процесс нанесен на карту, становится легче понять, сколько времени может потребоваться для завершения каждого процесса. Для любой повторяющейся деятельности лучше всего стандартизировать процесс.
Кроме того, документирование всех аналогичных действий в производственном процессе устанавливает основу на будущее, если произойдут изменения в маршрутах или сроках новых производственных процессов. Создание базовой линии помогает компаниям ускорить процесс планирования производства.
Выявление возможных проблем
Лучший способ предвидеть возможные проблемы в производственном процессе — это собрать исторические данные по аналогичным заданиям. Имея доступ к времени обработки, используемым материалам и сбоям, компания может применить метод анализа видов отказов и последствий для анализа возможностей рисков и снижения вероятности их возникновения. Благодаря анализу видов сбоев и их последствий, компания сможет глубоко изучить свои процессы и найти способы уменьшить влияние любых потенциальных проблем в работе.
Планы связи
Сотрудники должны знать обо всех планах по оптимизации производства, которые могут быть выполнены с помощью производственного программного обеспечения. План, связанные рабочие задания и производственные графики могут быть общими, чтобы сотрудники всегда знали о своих обязанностях и могли в любое время проверять производственную систему.
Оптимизация производства делает то, на что надеется каждый бизнес: постоянно производить качественную продукцию в оптимальные сроки, в соответствии с требованиями рынка.
Оптимизация производственного процесса в ваших руках!
Дайте экспертам подходящий инструмент для оптимизации производственных процессовДанные всегда рассказывают историю — все, что вам нужно сделать, это запечатлеть ее. А данные чрезвычайно важны для обработки и менеджеров активов. Его можно использовать для обнаружения аномалий в производительности процессов и активов, для тестирования и проверки гипотез, а также для решения проблем с производительностью. Обладая этой информацией, специалисты по технологическим процессам могут увеличить выход, контролировать качество продукции и снизить производственные затраты.
Специалисты по процессам разбираются в данных. У них есть повседневный опыт работы с этим. Это те, кто знает, что означает эта информация, например, какие датчики представляют интерес для исследования производственных показателей. При использовании аналитики самообслуживания эксперты по процессам действительно могут использовать данные в полной мере. Теперь вернемся к примеру с гонкой. Анализируя и понимая все данные, коуч (эксперт по процессам) может получить максимальную отдачу от вашего обучения (процесса) и улучшить вашу производительность (улучшить работу завода) и, следовательно, результат вашей гонки (производство продукции).Будь то тренеры или эксперты по процессам, им просто нужен правильный инструмент, который использует все данные для достижения максимальной производительности. Использование данных временных рядов в сочетании с контекстными даннымиДанные временного ряда создаются путем непрерывной записи значения в различные временные интервалы, которые могут составлять от минут до часов. Этот тип данных фиксируется в архиве и после агрегирования и обработки может быть проанализирован. Теперь с помощью аналитики самообслуживания эксперты по процессам могут использовать информацию для решения проблем и мониторинга процессов.И они могут сделать это без помощи специалиста по данным, потому что такой инструмент, как TrendMiner, использует распознавание образов и машинное обучение для выявления тенденций. Эксперты могут использовать эту информацию, чтобы получить представление о сложных производственных процессах и основывать свои решения на фактах, которые приведут к лучшим результатам производства.
Точно так же, как инструктор использовал контекстные данные для разработки программы, подходящей для вашего опыта и способностей, эксперты по процессам могут использовать контекстные данные для более эффективного управления предприятиями.Эти данные включают информацию о качестве, событиях технического обслуживания, эксплуатационных событиях, условиях окружающей среды и производительности процесса. Однако, поскольку этот тип данных обычно находится во внешних бизнес-приложениях, он изолирован или хранится отдельно в своих собственных приложениях и отдельно проверяется и контролируется другими группами. Кроме того, он обычно не используется вместе с данными временных рядов, что является огромной потерей потенциала.
В прошлом аналитика в основном вращалась вокруг использования данных временных рядов, но все данные о производственных процессах ценны и могут дать представление о производственных показателях.Фактически, чтобы работать и оставаться конкурентоспособными в сегодняшнем быстро меняющемся современном мире, компании могут использовать данные временных рядов в сочетании с контекстными данными. Возвращаясь к тренировкам для безумного триатлона. Тренер может использовать всю доступную информацию спортсмена для улучшения тренировок и повышения результативности соревнований, что приводит к гораздо более высокой вероятности успеха. Вы можете сделать то же самое со своим заводом — добиться оптимизации производственного процесса за счет интеграции данных.
Преобразование всех данных в актуальную информациюКак вы можете преобразовать все данные предприятия в фактическую информацию, чтобы улучшить работу? Ответ — такой инструмент, как TrendMiner.Во-первых, перед интеграцией других источников данных вам необходимо использовать исторические данные временных рядов, генерируемые датчиками, которые часто хранятся в архиваторах растений, но также могут храниться в базах данных SQL или озерах данных.
Тогда, используя структурную разбивку предприятия (структуру активов), вы получите очень хорошую основу для лучшего анализа производительности активов, что приведет к более глубокому пониманию эффективности процессов. TrendMiner дает вам несколько вариантов для создания структуры активов. Вы можете создать свой собственный или интегрировать его с платформой PI Assets от OSIsoft.Если у вас его нет, но есть какой-то тип файла, в котором хранятся ваши ресурсы, мы можем ввести этот файл в наше программное обеспечение, чтобы создать структуру ресурсов.Наконец, наше программное обеспечение может раскрывать события (контекстуализировать данные) из других бизнес-приложений. Ключевые — время начала и окончания событий для использования при анализе эксплуатационных характеристик. Вся эта информация обширна и ценна для анализа. Благодаря простой в использовании аналитической платформе самообслуживания, которая объединяет все данные вашего предприятия, эксперты могут получить 360-градусный обзор работы.
Посетите этот веб-семинар, чтобы получить более подробную информацию о том, как аналитика самообслуживания интегрирует данные: Как использовать интеграцию данных и оптимизировать самообслуживание аналитики
Обзор машинного обучения для оптимизации производственных процессов
Адиби М.А., Шахраби Дж. (2014) Основанный на кластеризации модифицированный алгоритм поиска переменной окрестности для задачи динамического планирования работы цеха. Int J Adv Manuf Technol 70 (9): 1955–1961
Google ученый
Адиби М.А., Зандие М., Амири М. (2010) Многоцелевое планирование динамического рабочего места с использованием переменного поиска по соседству. Expert Syst Appl 37 (1): 282–287
Google ученый
Ахмад Р., Камаруддин С. (2012) Обзор технического обслуживания по времени и по состоянию в промышленном применении. Comput Ind Eng 63 (1): 135–149
Google ученый
Apte C, Weiss S, Grout G Прогнозирование дефектов при производстве дисководов: пример крупномерной классификации.в: CAIA. Издательство IEEE Computer Society Press, Лос-Аламитос, стр. 212–218
Ариф Ф., Сурьяна Н., Хусин Б. (2013) Метод каскадного прогнозирования качества с использованием нескольких pca + id3 для многоступенчатой производственной системы. Процедура IERI 4: 201–207
Google ученый
Ассарзаде С., Горейши М. (2008) Моделирование и оптимизация процесса электроэрозионной обработки на основе нейронных сетей. Int J Adv Manuf Technol 39 (5-6): 488–500
Google ученый
Батиста Г., Прати Р., Монард М. (2004) Исследование поведения нескольких методов балансировки данных обучения машинного обучения. Информационный бюллетень ACM SIGKDD Explor 6 (1): 20–29
Google ученый
Bellini A, Filippetti F, Tassoni C, Capolino GA (2008) Достижения в диагностических методах для индукционных машин. IEEE Trans Ind Electron 55 (12): 4109–4126
Google ученый
Bouacha K, Terrab A (2016) Улучшение поведения при резком повороте с использованием гибридной модели nsga-ii и pso-nn. Int J Adv Manuf Technol 86 (9-12): 3527–3546
Google ученый
Braha D (2001) Интеллектуальный анализ данных для проектирования и производства: методы и приложения массовых вычислений, том 3. Springer, Boston
Google ученый
Колдер Дж., Сапсфорд Р. (2006) Статистические методы.В: Sapsford R, Jupp V (eds) Сбор и анализ данных. Sage Publications Ltd, Лондон, стр. 208–242
Цао В.Д., Ян С.П., Дин Л., Ма И (2016) Непрерывное принятие решений по оптимизации параметров процесса высокоскоростной зубофрезеровки с использованием алгоритма ibpnn / de. Int J Adv Manuf Technol 85 (9-12): 2657–2667
Google ученый
Кэссади Ч.Р., Кутаноглу Э. (2005) Интеграция планирования профилактического обслуживания и производственного планирования для одной машины.IEEE Trans Reliab 54 (2): 304–309
Google ученый
Цегларек Д., Пракаш П.К. (2012) Усовершенствованный кусочный метод наименьших квадратов для диагностики плохо подготовленных многостанционных сборок с совместимыми деталями. Proc Inst Mech Eng Часть B: J Eng Manuf 226 (3): 485–502
Google ученый
Чандрасекаран М., Муралидхар М., Кришна К.М., Диксит США (2010) Применение методов мягких вычислений в прогнозировании и оптимизации производительности обработки: обзор литературы.Int J Adv Manuf Technol 46 (5): 445–464
Google ученый
Чен Х., Бонинг Д. (2017) Подходы онлайн и инкрементального машинного обучения для повышения доходности ИС. В: Международная конференция IEEE / ACM по автоматизированному проектированию (ICCAD), 2017 г., Irvine, pp. 786–793
Chen SH, Perng DB (2011) Автоинспекция направленных текстур с использованием анализа главных компонентов. Int J Adv Manuf Technol 55 (9): 1099–1110
Google ученый
Chen WC, Fu GL, Tai PH, Deng WJ (2009) Оптимизация параметров процесса литья пластмасс под давлением с помощью мягких вычислений. Expert Syst Appl 36 (2): 1114–1122
Google ученый
Chen Z, Li X, Wang L, Zhang S, Cao Y, Jiang S, Rong Y (2018) Разработка гибридного алгоритма оптимизации роя частиц для оптимизации процесса многопроходного валкового измельчения. Int J Adv Manuf Technol 99 (1-4): 97–112
Google ученый
Cheng H, Chen H (2014) Оптимизация параметров онлайн в процессах сборки, контролируемых роботом. В: Международная конференция IEEE по робототехнике и автоматизации, 2014 г. (ICRA). Piscataway, pp 3465–3470
Chien CF, Chuang SC (2014) Структура для обнаружения первопричин системы субпакетной обработки для анализа больших данных производства полупроводников. IEEE Trans Semicond Manuf 27 (4): 475–488
Google ученый
Chien CF, Hsu CY, Chen PN (2013) Обнаружение и классификация неисправностей полупроводников для повышения доходности и интеллектуального производства. Flex Serv Manuf J 25 (3): 367–388
Google ученый
Chien CF, Liu CW, Chuang SC (2017) Анализ больших данных о производстве полупроводников для выявления первопричин отклонения с целью повышения урожайности. Int J Prod Res 55 (17): 5095–5107
Google ученый
Chien CF, Wang WC, Cheng J (2007) Интеллектуальный анализ данных для повышения доходности в производстве полупроводников и эмпирическое исследование. Expert Syst Appl 33 (1): 192–198
Google ученый
Colosimo BM, Pagani L, Strano M (2015) Снижение усилий по калибровке при оптимизации на основе женских ножек за счет объединения численных и экспериментальных данных. Struct Multidiscip Optim 51 (2): 463–478
Google ученый
Коппель Р., СП Абеллан-Небот, Силлер Х.Р., Родригес К.А., Гедеа Ф. (2016) Оптимизация адаптивного управления при микропереработке закаленных сталей — оценка подходов к оптимизации. Int J Adv Manuf Technol 84 (9-12): 2219–2238
Google ученый
Деметгуль М., Тансель И.Н., Таскин С. (2009) Диагностика неисправностей пневматических систем с помощью алгоритмов искусственной нейронной сети. Expert Syst Appl 36 (7): 10,512–10,519
Google ученый
Denkena B, Dittrich MA, Uhlich F (2016) Самооптимизирующийся процесс резки с использованием моделей процесса обучения. Процедура Technol 26: 221–226
Google ученый
Dhas JER, Kumanan S (2011) Оптимизация параметров сварки под флюсом с использованием нетрадиционных методов. Appl Soft Comput 11 (8): 5198–5204
Google ученый
Diao G, Zhao L, Yao Y (2015) Подход динамического контроля качества путем улучшения доминирующих факторов на основе улучшенного анализа главных компонентов.Int J Prod Res 53 (14): 4287–4303
Google ученый
Фернандес С., Понтес А.Дж., Виана Дж. К., Гаспар-Кунья А. (2018) Моделирование и оптимизация процесса литья под давлением: обзор. Adv Polym Technol 37 (2): 429–449
Google ученый
Franciosa P, Palit A, Vitolo F, Ceglarek D (2017) Быстрая диагностика многоступенчатого процесса сборки с соответствующими неидеальными деталями с использованием саморазвивающейся системы измерения.Процедуры CIRP 60: 38–43
Google ученый
Gao RX, Yan R (2011) Вейвлеты. Springer, Бостон
MATH Google ученый
Genna S, Simoncini A, Tagliaferri V, Ucciardello N (2017) Оптимизация процесса пескоструйной обработки для лучшего электроосаждения тонких пленок меди на алюминиевой подложке с помощью нейронной сети с прямой связью. Процедуры CIRP 62: 435–439
Google ученый
Гжегожевски П., Кочанский А., Кацпшик Дж. (2019) Мягкое моделирование в промышленном производстве. Springer, Берлин
Google ученый
Гупта А.К., Гунтуку С.К., Десу Р.К., Балу А. (2015) Оптимизация параметров поворота путем интеграции генетического алгоритма с опорной векторной регрессией и искусственными нейронными сетями. Int J Adv Manuf Technol 77 (1-4): 331–339
Google ученый
Harding JA, Shahbaz M, Kusiak A (2006) Интеллектуальный анализ данных в производстве: обзор. J Manuf Sci Eng 128 (4): 969–976
Google ученый
He QP, Qin SJ, Wang J (2005) Новый метод диагностики неисправностей с использованием направлений неисправности в дискриминантном анализе Фишера. AIChE J 51 (2): 555–571
Google ученый
Huang NE, Shen Z, Long SR, Wu MC, Shih HH, Zheng Q, Yen NC, Tung CC, Liu HH (1998) Разложение эмпирических мод и спектр Гильберта для нелинейного и нестационарного времени анализ серий.Proc R Soc A: Math Phys Eng Sci 454 (1971): 903–995
MathSciNet МАТЕМАТИКА Google ученый
Huang SH, Pan YC (2015) Автоматизированный визуальный контроль в полупроводниковой промышленности: обзор. Comput Ind 66: 1–10
Google ученый
Irani KB, Cheng J, Fayyad UM, Qian Z (1993) Применение машинного обучения в производстве полупроводников. Эксперт IEEE 8 (1): 41–47
Google ученый
Jäger M, Knoll C, Hamprecht FA (2008) Слабо контролируемое обучение классификатора для обнаружения необычных событий. IEEE Trans Image Process: Publ IEEE Signal Process Soc 17 (9): 1700–1708
MathSciNet Google ученый
Jian C, Gao J, Ao Y (2017) Автоматическое обнаружение дефектов поверхности стекла экрана мобильного телефона на основе машинного зрения. Appl Soft Comput 52: 348–358
Google ученый
Kamsu-Foguem B, Rigal F, Mauget F (2013) Правила горнодобывающей ассоциации по повышению качества производственного процесса. Expert Syst Appl 40 (4): 1034–1045
Google ученый
Кан П., Ли Х. Дж, Чо С., Ким Д., Парк Дж., Парк К. К., До С. (2009) Виртуальная метрологическая система для производства полупроводников. Expert Syst Appl 36 (10): 12,554–12,561
Google ученый
Kant G, Sangwan KS (2015) Прогностическое моделирование и оптимизация параметров обработки для минимизации шероховатости поверхности с использованием искусственной нейронной сети в сочетании с генетическим алгоритмом. Процедуры CIRP 31: 453–458
Google ученый
Карими М.Х., Асемани Д. (2014) Обнаружение поверхностных дефектов в плиточной промышленности с использованием методов цифровой обработки изображений: анализ и оценка. ISA Trans 53 (3): 834–844
Google ученый
Кашьяп С., Датта Д. (2015) Оптимизация параметров процесса литья пластмасс под давлением: обзор. Int J Plast Technol 19 (1): 1–18
Google ученый
Khakifirooz M, Chien CF, Chen YJ (2018) Байесовский вывод для добычи полупроводников, производство больших данных для повышения урожайности и интеллектуального производства для расширения возможностей Индустрии 4.0. Appl Soft Comput 68: 990–999
Google ученый
Хан А.А., Мойн Дж. Р., Тилбери Д. М. (2008) Виртуальная метрология и управление с обратной связью для процессов производства полупроводников с использованием рекурсивных частичных наименьших квадратов. J Управление процессами 18 (10): 961–974
Google ученый
Китайма С., Нацуме С. (2014) Многоцелевая оптимизация объемной усадки и усилия зажима для литья пластмасс под давлением путем последовательной приблизительной оптимизации. Практическая теория одновременного моделирования 48: 35–44
Google ученый
Китайма С., Онуки Р., Ямадзаки К. (2014) Снижение коробления с изменяемым профилем давления при литье пластмасс под давлением с помощью последовательной приблизительной оптимизации. Int J Adv Manuf Technol 72 (5): 827–838
Google ученый
Köksal G, Batmaz İ, Testik MC (2011) Обзор приложений интеллектуального анализа данных для повышения качества в обрабатывающей промышленности. Приложение Expert Syst 38 (10): 13,448–13,467
Google ученый
Конрад Б., Либер Д., Деус Дж. (2013) Стремление к производству без дефектов: интеллектуальное управление производством с помощью интеллектуального анализа данных в процессах непрерывной прокатки. В: Windt K (ed) Надежный производственный контроль, конспекты лекций по технологии производства. Springer, Berlin, pp. 215–229
Google ученый
Кришнан С.А., Самуэль Г.Л. (2013) Многоцелевая оптимизация скорости съема материала и шероховатости поверхности при токарной обработке проволокой с помощью электрического разряда.Int J Adv Manuf Technol 67 (9–12): 2021–2032
Google ученый
Кумар Н., Мастранджело С., Монтгомери Д. (2011) Иерархическое моделирование с использованием обобщенных линейных моделей. Qual Reliab Eng Int 27 (6): 835–842
Google ученый
Lei Y, He Z, Zi Y (2008) Новый подход к интеллектуальной диагностике неисправностей вращающегося оборудования. Expert Syst Appl 35 (4): 1593–1600
Google ученый
Liang Z, Liao S, Wen Y, Liu X (2017) Оптимизация параметров компонентов упрочнения суспензии гидроабразивного измельчения с помощью anfis на основе ортогонального эксперимента. Int J Adv Manuf Technol 90 (1-4): 831–855
Google ученый
Либер Д., Столпе М., Конрад Б., Деус Дж, Морик К. (2013) Прогнозирование качества взаимосвязанных производственных процессов на основе машинного обучения с учителем и без учителя. Процедуры CIRP 7: 193–198
Google ученый
Liggins II M, Hall D, Llinas J (2017) Справочник по объединению мультисенсорных данных: теория и практика. CRC Press, Boca Raton
Луо В., Рохас Дж., Гуан Т., Харада К., Нагата К. (2014) Обнаружение отказа сборок консольных защелок с использованием svms и rcbht. В: 2014 IEEE International Conference on Mechatronics and Automation (ICMA), Piscataway, pp 384–389
Majumder A (2015) Сравнительное исследование трех эволюционных алгоритмов в сочетании с нейросетевой моделью для оптимизации параметров процесса электроэрозионной обработки. .Proc Inst Mech Eng Часть B: J Eng Manuf 229 (9): 1504–1516
Google ученый
Masci J, Meier U, Ciresan D, Schmidhuber J, Fricout G (2012) Классификация стальных дефектов с помощью сверточных нейронных сетей с максимальным объединением. В: Международная совместная конференция по нейронным сетям 2012 г. (IJCNN). IEEE, Piscataway, pp 1–6
Mayne DQ (2014) Модель прогнозирующего контроля: последние разработки и перспективы на будущее. Automatica 50 (12): 2967–2986
MathSciNet МАТЕМАТИКА Google ученый
Ming W, Hou J, Zhang Z, Huang H, Xu Z, Zhang G, Huang Y (2015) Интегрированный ann-lwpa для оптимизации параметров резки в wedm. Int J Adv Manuf Technol 120 (1): 109
Google ученый
Mobley RK (2002) Введение в профилактическое обслуживание, 2-е изд. Баттерворт-Хайнеманн, Амстердам
Google ученый
Monostori L (1996) Подходы машинного обучения к производству.CIRP Ann Manuf Technol 45 (№2): 675–712
Google ученый
Montgomery DC (2013) Планирование и анализ экспериментов, 8-е изд. Уайли, Хобокен
Google ученый
Neugebauer R, Putz M, Hellfritzsch U (2007) Улучшенная технология и качество изготовления зубчатых колес с плоской и круглой прокаткой. CIRP Ann-Manuf Technol 56 (1): 307–312
Google ученый
Ниггеманн О., Лохвег В. (2015) О диагностике киберфизических производственных систем — современное состояние и повестка дня исследований. В: AAAI’15 Proceedings of the Twenty Девятая конференция AAAI по искусственному интеллекту. AAAI Press, pp 4119–4126
Norouzi A, Hamedi M, Adineh VR (2012) Моделирование прочности и оптимизация ультразвуковых сварных частей абс-ПММА с использованием методов искусственного интеллекта. Int J Adv Manuf Technol 61 (1-4): 135–147
Google ученый
Oh S, Han J, Cho H (2001) Интеллектуальная система управления технологическим процессом для повышения качества путем интеллектуального анализа данных в обрабатывающей промышленности. В: Braha D (ed) Data Mining for Design and Manufacturing, vol 3. Springer, Boston, pp 289–309
Google ученый
Park JK, Kwon BK, Park JH, Kang DJ (2016) Система визуализации на основе машинного обучения для проверки поверхностных дефектов. Int J Precis Eng Manuf-Green Technol 3 (3): 303–310
Google ученый
Пол А., Страно М. (2016) Влияние переменных процесса на газоформование и упрочнение стальных труб под давлением. J Mater Process Technol 228: 160–169
Google ученый
Peng A, Xiao X, Yue R (2014) Оптимизация параметров процесса для моделирования наплавленного осаждения с использованием методологии поверхности отклика в сочетании с системой нечеткого вывода. Int J Adv Manuf Technol 73 (1-4): 87–100
Google ученый
Perng DB, Chen SH (2011) Автоинспекция направленных текстур с использованием дискретного косинусного преобразования. Int J Prod Res 49 (23): 7171– 7187
Google ученый
Pfrommer J, Zimmerling C, Liu J, Kärger L, Henning F, Beyerer J (2018) Оптимизация параметров производственного процесса с использованием глубоких нейронных сетей в качестве суррогатных моделей. Процедуры CIRP 72: 426–431
Google ученый
Queipo NV, Haftka RT, Shyy W, Goel T, Vaidyanathan R, Kevin Tucker P (2005) Анализ и оптимизация на основе суррогатов. Prog Aerosp Sci 41 (1): 1–28
MATH Google ученый
Рао Р.В., Павар П.Дж. (2009) Моделирование и оптимизация технологических параметров электроэрозионной обработки проволоки. Proc Inst Mech Eng Часть B: J Eng Manuf 223 (11): 1431–1440
Google ученый
Ren R, Hung T, Tan KC (2018) Общий подход, основанный на глубоком обучении, для автоматизированного контроля поверхности. IEEE Trans Cybern 48 (3): 929–940
Google ученый
Rodger JA (2018) Достижения в слиянии мультисенсорной информации: нечеткий статистический предиктор вязкости Маркова – Калмана для анализа показателей потока, диффузии, скорости, температуры и времени кислорода в cpap. Expert Syst 35 (4): e12,270
Google ученый
Родригес А., Борн Д., Мейсон М., Россано Г. Ф., Ван Дж. (2010) Обнаружение сбоев в сборке: анализ сигнатуры силы. В: Конференция IEEE 2010 по науке и технике автоматизации (CASE). Piscataway, NJ
Rong Y, Zhang G, Chang Y, Huang Y (2016) Интегрированная оптимизационная модель лазерной пайки с помощью машины с экстремальным обучением и генетического алгоритма. Int J Adv Manuf Technol 87 (9): 2943–2950
Google ученый
Rong-Ji W, Xin-hua L, Qing-ding W, Lingling W. (2009) Оптимизация параметров процесса для селективного лазерного спекания на основе нейронной сети и генетического алгоритма. Int J Adv Manuf Technol 42 (11-12): 1035–1042
Google ученый
Сагироглу С., Синанц Д. (2013) Большие данные: обзор. В: 2013 Международная конференция по технологиям и системам совместной работы (CTS). IEEE, pp. 42–47
Сараванан Н., Рамачандран К.И. (2010) Диагностика неисправности коробки передач с использованием дискретного вейвлет-преобразования (dwt) для выделения и классификации признаков с использованием искусственной нейронной сети (ann).Expert Syst Appl 37 (6): 4168–4181
Google ученый
Scattolini R (2009) Архитектуры для упреждающего управления распределенными и иерархическими моделями — обзор. J Управление процессами 19 (5): 723–731
Google ученый
Scholz-Reiter B, Weimer D, Thamer H (2012) Автоматизированный контроль поверхности микродеталей, подвергнутых холодной штамповке. CIRP Ann 61 (1): 531–534
Google ученый
Сенн М., Линк Н. (2012) Универсальная модель для наблюдения за скрытым состоянием в адаптивном управлении процессом. Int J Adv Intell Syst 4 (3-4): 245–255
Google ученый
Senn M, Link N, Gumbsch P (2013) Оптимальное управление процессом посредством отслеживания состояния на основе функций по цепочкам процессов. В: Материалы 2-го Всемирного конгресса по интегрированной вычислительной инженерии материалов (ICME), стр. 69–74
Google ученый
Shahrabi J, Adibi MA, Mahootchi M (2017) Подход с подкреплением к оценке параметров при динамическом планировании рабочих мест. Comput Ind Eng 110: 75–82
Google ученый
Sharp M, Ak R, Hedberg T (2018) Обзор перспективного использования и развития машинного обучения в интеллектуальном производстве. J Manuf Syst 48: 170–179
Google ученый
Shewhart WA (1925) Применение статистики как вспомогательного средства для поддержания качества производимой продукции.J Am Stat Assoc 20 (152): 546
Google ученый
Ши Х, Гао Й, Ван Х (2010) Оптимизация параметров процесса литья под давлением с использованием интегрированной модели искусственной нейронной сети и метода функции ожидаемого улучшения. Int J Adv Manuf Technol 48 (9): 955–962
Google ученый
Shi H, Xie S, Wang X (2013) Метод оптимизации коробления для литья под давлением с использованием искусственной нейронной сети со стратегией оценки параметрической выборки.Int J Adv Manuf Technol 65 (1): 343–353
Google ученый
Шин Х.Дж., Эом Д.Х., Ким С.С. (2005) Машины с вектором поддержки одного класса — приложение для обнаружения и классификации сбоев машин. Comput Ind Eng 48 (2): 395–408
Google ученый
Силва Дж. А., Абеллан-Небот СП, Силлер Х. Р., Гедеа-Элизальде Ф. (2014) Система оптимизации адаптивного управления для минимизации производственных затрат при операциях твердого фрезерования.Int J Comput Integr Manuf 27 (4): 348–360
Google ученый
Сиванага Маллесвара Рао С., Венката Рао К., Хемачандра Редди К., Парамесвара Рао CVS (2017) Прогнозирование и оптимизация технологических параметров при электроэрозионной обработке проволокой для быстрорежущей стали (hss). Int J Comput Appl 39 (3): 140–147
Google ученый
Sorensen LC, Andersen RS, Schou C, Kraft D (2018) Автоматическое обучение параметрам для удобного обучения промышленных коллаборативных роботов.В: Международная конференция IEEE по промышленной технологии (ICIT), 2018, Piscataway, pp 87–92
Srinivasu DS, Babu NR (2008) Стратегия адаптивного управления процессом гидроабразивной резки с интеграцией систем технического зрения мониторинг и нейрогенетическая стратегия контроля. Int J Adv Manuf Technol 38 (5-6): 514–523
Google ученый
Стефатос Г., Бенхамза А. (2010) Подход динамического анализа независимых компонентов для обнаружения и диагностики неисправностей.Expert Syst Appl 37 (12): 8606–8617
Google ученый
Sterling D, Sterling T, Zhang Y, Chen H (2015) Оптимизация параметров сварки на основе байесовского алгоритма регрессии процесса по Гауссу. В: Международная конференция IEEE по науке и технике автоматизации (CASE), 2015 г., Piscataway, pp. 1490–1496
Stoll A, Pierschel N, Wenzel K, Langer T. (2019) многочисленные переменные процесса и критерии качества.В: Машинное обучение для киберфизических систем. Springer, pp 77–86
Sun A, Jin X, Chang Y (2017) Исследование модели оптимизации процесса лазерной обработки с помощью электролиза с микрозазорами на основе нейронной сети bp и колонии муравьев. Int J Adv Manuf Technol 88 (9-12): 3485–3498
Google ученый
Цай Д.М., Лай С.К. (2008) Обнаружение дефектов на периодически структурированных поверхностях с использованием независимого компонентного анализа.Распознавание образов 41 (9): 2812–2832
MATH Google ученый
Валаванис И., Космопулос Д. (2010) Обнаружение и классификация многоклассовых дефектов на радиографических изображениях сварных швов с использованием геометрических и текстурных элементов. Expert Syst Appl 37 (12): 7606–7614
Google ученый
Валлехо А.Дж., Моралес-Менендес Р. (2010) Экономичная система диспетчерского управления периферийным фрезерованием с использованием hsm.Annu Rev Control 34 (1): 155–162
Google ученый
Венката Рао К., Мурти PBGSN (2018) Моделирование и оптимизация вибрации инструмента и шероховатости поверхности при растачивании стали с использованием rsm, ann и svm. J Intell Manuf 29 (7): 1533–1543
Google ученый
Виджаярагаван А., Дорнфельд Д. (2010) Автоматизированный энергетический мониторинг станков. CIRP Ann 59 (1): 21–24
Google ученый
Ван Ч. (2008) Распознавание структур дефектов полупроводников с использованием пространственной фильтрации и спектральной кластеризации. Expert Syst Appl 34 (3): 1914–1923
Google ученый
Ван Г.Г., Шан С. (2007) Обзор методов метамоделирования в поддержку оптимизации инженерного проектирования. J Mech Des 129 (4): 370
Google ученый
Ван Дж, Ма И, Чжан Л., Гао RX, Ву Д. (2018) Глубокое обучение для интеллектуального производства: методы и приложения.J Manuf Syst 48: 144–156
Google ученый
Веймер Д., Шольц-Райтер Б., Шпитальни М. (2016) Разработка архитектур глубоких сверточных нейронных сетей для автоматического выделения признаков в промышленном контроле. CIRP Ann 65 (1): 417–420
Google ученый
Weiss SM, Baseman RJ, Tipu F, Collins CN, Davies WA, Singh R, Hopkins JW (2010) Интеллектуальный анализ данных на основе правил для повышения доходности в производстве полупроводников.Appl Intell 33 (3): 318–329
Google ученый
Weiss SM, Dhurandhar A, Baseman RJ (2013) Улучшение контроля качества путем раннего прогнозирования производственных результатов. В: Материалы 19-й международной конференции ACM SIGKDD по обнаружению знаний и интеллектуальному анализу данных. ACM, pp 1258–1266
Weiss SM, Dhurandhar A, Baseman RJ, White BF, Logan R, Winslow JK, Poindexter D (2016) Непрерывное прогнозирование производственных показателей на протяжении всего производственного цикла.J Intell Manuf 27 (4): 751–763
Google ученый
Wu Z, Huang NE (2009) Ансамблевое разложение эмпирических мод: метод анализа данных с использованием шума. Adv Adapt Data Anal 01 (01): 1–41
Google ученый
Wuest T, Weimer D, Irgens C, Thoben KD (2016) Машинное обучение в производстве: преимущества, проблемы и приложения. Prod Manuf Res 4 (1): 23–45
Google ученый
Xu G, Yang Z (2015) Многокритериальная оптимизация параметров процесса литья пластмасс под давлением с помощью мягких вычислений и анализа корреляции серого. Int J Adv Manuf Technol 78 (1-4): 525–536
Google ученый
Yin S, Ding SX, Xie X, Luo H (2014) Обзор основных подходов к мониторингу промышленных процессов, основанных на данных. IEEE Trans Ind Electron 61 (11): 6418–6428
Google ученый
Юн Дж. П., Чой округ Колумбия, Чон Ю. Дж., Пак С., Ким С. В. (2014) Система контроля дефектов стальной катанки, произведенной методом горячей прокатки. Int J Adv Manuf Technol 70 (9-12): 1625–1634
Google ученый
Юсуп Н., Заин А.М., Хашим СЗМ (2012) Эволюционные методы оптимизации параметров обработки: обзор и недавние приложения (2007–2011). Expert Syst Appl 39 (10): 9909–9927
Google ученый
Заин А.М., Харон Х., Шариф С. (2008) Обзор метода ga для оптимизации шероховатости поверхности в процессе фрезерования. 2008 Int Sympos Inf Technol 4: 1–6
Google ученый
Заин А.М., Харон Х., Шариф С. (2011) Оптимизация технологических параметров при абразивной гидроабразивной обработке с использованием интегрированного sa – ga. Appl Soft Comput 11 (8): 5350–5359
Google ученый
Zain AM, Haron H, Sharif S (2012) Интегрированный ann – ga для оценки минимального значения производительности обработки. Int J Prod Res 50 (1): 191–213
MATH Google ученый
Zhang L, Jia Z, Wang F, Liu W (2010) Гибридная модель, использующая вспомогательную векторную машину и многоцелевой генетический алгоритм для оптимизации параметров обработки в микро-EDM. Int J Adv Manuf Technol 51 (5-8): 575–586
Google ученый
Zhang W, Jia MP, Zhu L, Yan XA (2017) Всесторонний обзор методов вычислительного интеллекта для мониторинга состояния оборудования и диагностики неисправностей. Chin J Mech Eng 30 (4): 782–795
Google ученый
Zhao T, Shi Y, Lin X, Duan J, Sun P, Zhang J (2014) Прогнозирование шероховатости поверхности и оптимизация параметров в процессе шлифования и полировки для ibr авиационного двигателя. Int J Adv Manuf Technol 74 (5-8): 653–663
Google ученый
Ключевые факторы оптимизации производственных линий, процессов и цепочек поставок
При внедрении нового продукта следует ли вам работать с существующей цепочкой поставок, чтобы оптимизировать затраты на детали для обоих продуктов, или добавить дополнительных партнеров по цепочке поставок для оптимизации качества и эффективности нового продукта? В этой статье обсуждаются плюсы и минусы каждого варианта и предлагаются предложения, которые помогут вам в процессе принятия решений.
Вы достигли ключевого рубежа:
Вы разработали новый передовой продукт и хотели бы начать его производство наряду с более стабильными и простыми в производстве линейками продуктов. И теперь вам нужно принять решение.
Следует ли вам работать с существующей цепочкой поставок, чтобы оптимизировать затраты на детали для обоих продуктов, или добавить дополнительных партнеров по цепочке поставок для оптимизации качества и эффективности нового продукта?
Согласно исследованию тенденций в области производственного аутсорсинга Arena:
- 42% производителей планировали добавить один или несколько КМ для диверсификации или увеличения производственных мощностей
- 46.9% производителей планировали выводить новые продукты на свой текущий рынок
- 39,7% производителей планировали вывод новых продуктов на новый рынок
Ключевые факторы в процессе принятия решений
- Доступные ресурсы — Есть ли у вас время и деньги, необходимые для управления несколькими поставщиками цепочки поставок для каждой линейки продуктов?
- Организационные приоритеты — Вы бы предпочли оптимизировать процесс проектирования или оптимизировать затраты?
- Жизненный цикл цепочки поставок — Есть ли у вашей нынешней цепочки поставок место для развития вместе с линейками продуктов?
- Отношения с поставщиками — Сможет ли ваш текущий поставщик помочь вам оптимизировать каждую линейку продуктов? Ваш нынешний поставщик видит вас в качестве приоритетного клиента?
- Риск — Можете ли вы справиться с рисками, связанными с добавлением нового поставщика?
Взвесьте варианты перед принятием решения
Вариант А.
Оптимизируйте стоимость деталей, работая с единой цепочкой поставок.
Вариант Б.
Найдите лучшую цепочку поставок для каждой линейки продуктов.
Вариант A: придерживайтесь существующей цепочки поставок для оптимизации затрат
Почему вам стоит рассмотреть возможность выхода за пределы существующей цепочки поставок
Обычно при запуске нового продукта обращаются к альтернативным партнерам по цепочке поставок. Вы никогда не должны чувствовать себя привязанным к определенной производственной вертикали просто потому, что ваш существующий продукт использует ее — подумайте о проведении экономического и технического анализа осуществимости, чтобы решить, подходит ли ваша текущая цепочка поставок наилучшим образом для нового продукта.
В некотором смысле это решение напоминает то, что вы можете принять в своей личной жизни. Тот факт, что вы заключили контракт с ландшафтной компанией на установку и обслуживание системы полива и дождевания, не означает, что вам придется использовать их, если вы решите построить бассейн позже (но если у вас был хороший опыт работы с первой компанией, вы естественно будет рассматривать их как партнера для нового проекта.)
Когда это может сработать для вас:
- У вас есть крупносерийные продукты низкой сложности с одинаковыми инструментами, сырьем или процедурами сборки Пример: если компания, производящая коробки, предлагает коробки нового размера или формы, имеет смысл использовать ту же цепочку поставок, чем найти кого-нибудь нового, кто сделает то же самое
- Вашей организации не хватает ресурсов для управления новыми партнерами в цепочке поставок
- Ваш текущий партнер по цепочке поставок может предложить разнообразные решения и имеет возможности для роста
- Вы уверены в своей способности создавать резервные копии, если что-то случится с вашим текущим партнером
Возможные преимущества | Риски |
---|---|
Простота | Пониженная стабильность |
Снижение затрат на детали из-за оптовых закупок | Упущенная возможность для инноваций |
Снижение затрат на управление и необходимых ресурсов | Повышенная зависимость от ваших текущих партнеров по цепочке поставок |
Возможности для развития налаженных отношений | Не лучшая команда для нового продукта |
Работайте с единой цепочкой поставок, чтобы уменьшить количество ошибок и упростить
Наличие единой цепочки поставок упрощает задачу.Управление меньшим количеством личностей и передач на протяжении всего производственного процесса может уменьшить количество ошибок и облегчить нагрузку на вашу управленческую команду.
Передавать вещи новому поставщику может быть рискованно, и вы можете не получить тот уровень обслуживания, который вам обещали при первоначальной продаже. Хотя новый поставщик может давать большие обещания, вы уже знаете, чего ожидать от существующей цепочки поставок, поэтому в краткосрочной перспективе придерживаться того, что вы знаете, менее рискованно.
Используйте своего текущего поставщика, чтобы воспользоваться эффектом масштаба
Увеличение объема продаж с вашим текущим поставщиком может привести к значительному снижению затрат за счет оптовых цен.Если вы используете одинаковые детали во всех своих продуктовых линейках, работа с единой цепочкой поставок значительно упрощает определение дублирования ваших деталей и координацию закупок, чтобы получить стимулы на основе вашего большего объема.
«Новое» не всегда улучшается
Если вы все же добавите вторую цепочку поставок, вы не только потеряете возможность для оптового ценообразования, но и затраты могут быстро возрасти — не только начальные затраты на установку, но и дополнительные затраты на управление, которые вы понесете даже после введения новой поставщик запущен и работает.Несколько цепочек поставок могут быть лучшим способом оптимизации дизайна продукта, но стресс, связанный с управлением несколькими цепочками, иногда может отвлечь ваше внимание от продукта.
Вариант Б. Найдите лучшую цепочку поставок для каждой линейки продуктов
Когда это может сработать для вас:
- Компоненты и производственные процессы вашей текущей и новой линейки продуктов сильно различаются
- У вашей управленческой команды есть возможность взять на себя дополнительные обязанности
- Ваши клиенты очень чувствительны к качеству
- Вы хотите снизить общий риск цепочки поставок
- У вас нет прочных отношений с вашими текущими партнерами по цепочке поставок
Возможные преимущества | Риски |
---|---|
Снижение риска цепочки поставок | Меньше возможностей для оптовых цен |
Лучше согласованные партнеры по цепочке поставок | Дополнительные расходы на установку и управление |
Совместные компетенции по каждому продукту | Повышенная сложность |
Лучшее время доставки и более высокое качество | |
Повышенная гибкость и инновации |
Диверсификация для минимизации долгосрочного риска
Несмотря на то, что внесение больших изменений, таких как добавление поставщика, сопряжено с риском, диверсифицированная цепочка поставок снижает ваш риск в долгосрочной перспективе.
В конце концов, трава может быть и зеленее
Добавление новой линейки продуктов — отличный шанс попробовать работать с другой цепочкой поставок, особенно если вы недовольны своей нынешней командой или работаете с ними долгое время. Кто знает? Если новые поставщики действительно впечатляют вас, возможно, вам имеет смысл передать весь свой бизнес новому поставщику, когда ваш продукт достигнет зрелости.
Выберите «лучшее», чтобы получить наилучшие результаты
Понятие «лучший» для каждой линии подразумевает очевидные выгоды.Наличие поставщиков, чьи компетенции соответствуют потребностям вашего продукта, может привести к более быстрой доставке, более высокому качеству и снижению затрат, что, в свою очередь, может привести к повышению удовлетворенности клиентов и увеличению прибыли.
Воспользуйтесь возможностью внедрить инновации
Стадии прототипа и раннего производства — отличное время для встряски. В жизненном цикле вашей компании бывает несколько случаев, когда у вас есть возможность по-настоящему внедрять инновации, поэтому максимально используйте их, когда они появятся. Даже если вы довольны своим текущим поставщиком, добавление новой цепочки поставок встряхнет ситуацию и позволит вывести новые идеи для вашего продукта и процесса.Придерживаясь одного поставщика, вы упускаете возможность найти новый и лучший способ решения задач.
Какие ошибки связаны с затратами при разработке продукта?
Одна ошибка в дизайне продукта может привести к проблемам с качеством или производством — задержка выпуска следующего продукта и многомиллионные эксплуатационные расходы.
Наш калькулятор затрат включает в себя видимые затраты, такие как командные расходы и инструменты, а также стратегический анализ влияния на затраты из-за упущенных рыночных возможностей и неудовлетворенности клиентов.
Чтобы рассчитать стоимость ошибок при разработке продукта, просто введите данные о своем бизнесе, выберите задачу и посмотрите, как в реальном мире повлияет на затраты, как это было подтверждено нашими клиентами.
Рассчитать стоимость
Резюме:
Вы можете захотеть, чтобы ваша текущая цепочка поставок управляла вашей новой линейкой продуктов, если:
- Вашей внутренней управленческой команде не хватает доступности и компетентности, чтобы привлекать новых партнеров по цепочке поставок
- У вас есть крупносерийные изделия низкой сложности, в которых используются аналогичные инструменты, сырье или процедуры сборки
- Ваш текущий партнер по цепочке поставок может предложить разнообразные решения и имеет возможности для роста
- Вы уверены в своей способности создавать резервные копии, если что-то случится с вашим текущим партнером
Рассмотрите возможность работы с новой командой цепочки поставок для управления вашей новой линейкой продуктов, если:
- Компоненты и производственные процессы вашей новой и текущей линейки продуктов сильно отличаются
- У вашей управленческой команды есть возможность взять на себя дополнительные обязанности
- Вы не можете позволить себе качественную комбинацию
- Вы хотите снизить общий риск цепочки поставок
- У вас нет крепких отношений с вашими нынешними партнерами
Советы по работе
Если вы продолжите работу со своим текущим партнером по цепочке поставок и представите новый продукт, возможно, имеет смысл использовать новый продукт как козырную карту для получения лучших условий или как способ продемонстрировать свою веру в партнера и улучшить отношения.Помните, что счастливые партнеры работают лучше и, в конечном итоге, повышают уровень удовлетворенности клиентов.
Если вы остаетесь со своими нынешними поставщиками, подумайте над этим — не кладите все яйца в одну корзину только потому, что это путь наименьшего сопротивления. Когда у вас хорошие отношения со своей цепочкой поставок, легко предположить, что нет ничего лучше, но, возможно, стоит провести комплексную проверку и изучить потенциал новых партнеров.
Если вы диверсифицируетесь, начинайте с малого — чем меньше вы играете, тем меньше можете проиграть.Когда вы имеете дело с новыми партнерами, вы должны быть осторожны с тем, как быстро вы инвестируете. Прежде чем прыгнуть, опустите палец ноги в воду и посмотрите, каково это.
Если вы планируете инвестировать в новую цепочку поставок, подумайте, сколько единиц придется продать, чтобы покрыть ваши невозвратные затраты. Не бросайтесь в новую производственную среду, не убедившись, что есть возможность окупить ваши первоначальные затраты. Следите за ходом продаж — в то время как новый поставщик будет давать большие обещания по развитию вашего бизнеса, важно свести коммерческое предложение к холодным и неопровержимым фактам.
И, независимо от вашего решения, подумайте о решениях для совместной работы в цепочке поставок, которые помогут вашим внутренним командам общаться в режиме реального времени с внешними поставщиками. Современные решения для управления жизненным циклом продукта (PLM) и системы управления качеством (QMS) предоставляют облачные решения, позволяющие держать всех на одной странице.
(PDF) Обзор оптимизации производственного процесса
Заведующий производственной деятельностью.
Как правило, оптимизация производственной деятельности
не носит гибкого характера, учитывая
условий с данного момента, без
с учетом возможных возмущений или других влияний
.
Энергоэффективность и воздействие на окружающую среду производственных процессов
должны рассматриваться как минимум как ограничение
, если они даже не рассматриваются как объективная функция
в соответствии с действующими законодательными требованиями.
В будущих исследованиях будет предложена целостная методология подхода
к оптимизации производственных процессов. Целостное слово
относится к обоим критериям оптимизации и
моменту применения оптимизации в производственных процессах
.Предполагается, что этот подход позволит улучшить характер гибкости на
.
СПИСОК ЛИТЕРАТУРЫ
[1] И. Попеску, «Оптимизация процесса резки» («Оптимизация процесса резки
») Скрисул Романеск, Крайова, 1987.
[2] Г. Фрумушану и А. Епуряну, «Холистический подход к проблеме оптимизации
в производстве », Международный журнал
Materials, Mechanics and Manufacturing, vol.4, вып. 1, стр. 31-35,
2016.
[3] Г. Фрумушану и А. Епуряну, «Энергетически оптимальное программирование и планирование производственных операций
», Материаловедение и
Engineering, vol. 147, pp. 022-028-35, 2016.
[4] Д. Геласе, Л. Дащиевич, В. Маринеску, А. Епуряну, «Метод
для управления производственной системой на заказ на на основе
оценки рентабельности », Int J Adv Manuf Technol, vol.65, pp.
1439-1458, 2013.
[5] М. Дай, Д. Тан, Ю. Сюй и В. Д. Ли, «Энергетическое интегрированное планирование процессов
и составление графиков для мастерских», в Proc.
Институт инженеров-механиков, Часть B: Технический журнал
Производство, т. 229, pp. 13–26, 2015.
[6] CC Negrete, JDC Nájera и JCM Valenzuel, «Оптимизация параметров резания
для минимизации энергопотребления при токарной обработке
стали AISI 1018 при постоянной скорости съема материала с использованием прочная конструкция
», Int J Adv Manuf Technol, vol.83, pp. 1341–1347, 2016.
[7] R. Rentsch, C. Heinzel и E. Brinksmeier, «Искусственный интеллект для
, энерго- и ресурсосберегающего проектирования производственной цепочки и
операций», в Proc. . CIRP ICME’14-9-я конференция по интеллектуальным вычислениям в машиностроении
, стр. 139-144, 2015.
[8] Дж. Ма, Х. Ге, С.И. Чанг и С. Лей, «Оценка резки энергия
потребление и энергоэффективность при обработке стали 4140 », Int J
Adv Manuf Technol, vol.74, pp. 1701–1708, 2014.
[9] А. Коста, Дж. Челано и С. Фичера, «Оптимизация многопроходной экономики
разворота с помощью метода гибридной оптимизации роя частиц
», Int J Adv Manuf Technol, т. 53, стр. 421–433, 2011.
[10] Д. Петкович и М. Радованович, «Использование генетических алгоритмов для оптимизации процесса токарной обработки
», Технический журнал
Исследования и исследования, вып. 19, нет. 1, стр.47–55, 2013.
[11] Р. Усубаматов, З.М. Заин, Т.С. Син, С. Капаева, «Оптимизация
процессов многоинструментальной обработки с одновременным действием», Int J Adv
Manuf Technol, vol. . 82, стр. 1227–1239, 2015.
[12] С.Р. Дас, Р.П. Наяк и Д. Дхупал, «Оптимизация параметров резания
по износу инструмента, температуре поверхности заготовки и материалу
Скорость удаления при токарной обработке AISI. Сталь D2 », Международный журнал
инженерных исследований и технологий, вып.1, вып. 5, pp. 1-10,
2012.
[13] М. Джанардхан и А.Г. Кришна, «Многоцелевая оптимизация параметров резания
для шероховатости поверхности и скорости съема металла при плоском шлифовании
с использованием ответной поверхности. методология », Международный
Журнал достижений в области инженерии и технологий, вып. 3, № 1, стр.
270-283, 2012.
[14] О. Зерти, М.А. Яллезе, Р. Хеттаби, К. Чауи, Т. Мабруки,
«Оптимизация проекта для минимальных технологических параметров при сухая токарная обработка стали AISI D3 по методу Тагучи
», Int J Adv Manuf
Technol, 2016.
[15] Т. Х. Бхуйян, И. Ахмед, «Оптимизация параметров резания в процессе токарной обработки
», Журнал производственной инженерии, вып. 16, нет. 2,
pp. 11-19, 2013.
[16] М. Винтер, В. Ли, С. Кара и К. Херрманн, «Поэтапный подход к
снижает затраты и воздействие на окружающую среду процессов измельчения. ”Int
J Adv Manuf Technol, vol. 71, pp. 919-931, 2013.
[17] W. Yang, Y. Guo и W. Liao, «Многоцелевая оптимизация многопроходного торцевого фрезерования
с использованием интеллектуального роя частиц», Int J Adv.
Мануф Технол, т.56, pp. 429-443, 2011.
[18] Ф. Кюблер, Дж. Бёнер и Р. Штайнхильпер, «Эффективность использования ресурсов
Оптимизацияпроизводственных процессов с использованием эволюционных вычислений
: случай поворота», Процедуры CIRP 29, pp. 822-827, 2015.
[19] А. Икбал, Х.К. Чжан, Л.Л. Конг и Гулам Хуссейн, «Основанная на правилах система
для компромисса между потреблением энергии, сроком службы инструмента и
.производительности в процессе обработки », J Intell Manuf, т.26, pp.
1217-1232, ноябрь 2013 г.
[20] MHF Al Hazza и EYT Adesta, «Оптимизация энергопотребления
в токарном процессе с ЧПУ с использованием многоцелевого генетического алгоритма
», Advanced Materials Research, vol. . 576, pp. 92-98, 2012.
[21] V. Pare, G. Agnihotri, and C.M. Кришна, «Оптимизация условий резания
в процессе концевого фрезерования с использованием подхода оптимизации скопления частиц
», Международный журнал механики и промышленности
Engineering, vol.1, вып. 2, стр. 21-25, 2011.
[22] Дж. Ван, «Нейросетевой подход к многоцелевой резке.
Оптимизация параметровна основе нечеткой информации о предпочтениях»,
Comput Ind Eng, vol. 25, pp. 389-392, 1993.
[23] Ф. Шроуф, Й.О. Мере, А.Г. Санчес и М.О. Майер, «Оптимизация
планирования производства отдельной машины для минимизации общих затрат на потребление энергии
», Журнал чистого производства, т.67, pp.
197-207, 2014.
[24] Д. Танг, М. Дай, М.А. Салидо и А. Гирет, «Энергосберегающее динамическое планирование
для гибкого производственного процесса с использованием улучшенных частиц.
Оптимизация роя, Компьютеры в промышленности, т. 81, pp. 82-95, 2016.
[25] Р. Чжан и Р. Чион, «Решение задачи планирования
энергоэффективного цеха
: многоцелевой генетический алгоритм с расширенным локальным поиском
для минимизация общего взвешенного опоздания и
общего потребления энергии », Дж. Чистое производство, т.112, pp.
3361-3375, 2016.
[26] Y. He, Y. Li, T. Wu и JW Sutherland, «Энергосберегающий метод оптимизации
для выбора и эксплуатации станков
последовательность действий в цехах гибкой механической обработки », Journal of Cleaner
Production, vol. 87, pp. 245-254, 2015.
[27] Я. Лю и З. Фенг, «Двухмашинное планирование без ожидания поточного цеха с эффектом обучения
и выпуклым временем обработки, зависящим от ресурсов»,
Journal чистого производства, т.75, pp. 170-175, 2014.
[28] З. Урук, Х. Гультекин и М.С. Актюрк, «Двухмашинное планирование
с гибкими операциями и контролируемым временем обработки», журнал
по чистому производству. , т. 40, pp. 639-653, 2013.
[29] CY Cheng и LW Huang, «Минимизация общего раннего и
опозданий за счет несвязанного параллельного машинного планирования с использованием распределенного управления временем выпуска
», J of Cleaner Production, vol. .137,
pp. 1543-1552, 2016.
[30] Л. Чжан, X. Ли, Л. Гао и Г. Чжан, «Динамическое изменение графика в FMS
, которое одновременно учитывает потребление энергии и график
.эффективности », Int J Adv Manuf Technol, vol. 87, pp. 1387-1399, 2016.
[31] Дж. Ян, Л. Ли, Ф. Чжао, Ф. Чжан и К. Чжао, «Многоуровневый подход к оптимизации
для энергосберегающих гибких flow shop
scheduling, Journal of Manufacturing Systems, vol.42, стр. 1-10,
2016.
[32] Дж. Мун, К. Шин и Дж. Парк, «Оптимизация производства
планирование с зависящим от времени и машинно-зависимым электричеством
Затраты на промышленное производство. энергоэффективность », Int J Adv Manuf Technol, vol. 68,
pp. 523-535, 2013.
[33] S. Wang, X. Lu, X.X. Ли и В.Д. Ли, «Системный подход к планированию процессов
и оптимизации расписания для устойчивой обработки
», Journal of Cleaner Production, vol.87, pp. 914-929,
2015.
[34] Q. Lihong, L. Shengping, «Улучшенный генетический алгоритм для интегрированного планирования и составления процессов
», Int J Adv Manuf Technol,
vol. . 58, pp. 727-740, 2012.
[35] М. Кумар и С. Раджотия, «Интеграция планирования процессов и составления графиков
в среде рабочего цеха», Int J Adv Manuf Technol, vol.
28, pp. 109-116, 2006.
[36] М. Дай, Д. Тан, Ю. Сюй и В.Ли, «Энергетический интегрированный процесс
планирования и составления графиков для мастерских по ремонту», в Proc. IMechE Часть B: J
Engineering Manufacture, vol. 229, pp. 13-26, 2014.
[37] Г.А. Акель, М.Ф. Аусаф, X. Ли и Л. Гао, «IA New Priority-Sort
Алгоритм оптимизации на основедля интегрированного планирования процессов» и
International Journal моделирования и оптимизации, Vol. 7, No. 3, июнь 2017 г.
Технология оптимизации производства: Fujitsu США
Сегодня в производстве жесткая рыночная конкуренция и сложные экономические условия делают производственные ошибки и отходы недопустимыми.Поэтому жизненно важно, чтобы производители открывали большую производительность и новую эффективность. Однако преодолеть проблемы повышения гибкости и скорости производства при сохранении низких затрат непросто.
Как правило, производственные производственные процессы являются сложными, и эта сложность означает, что узкие места часто возникают и остаются незамеченными, что приводит к снижению эффективности, накоплению запасов и потере пропускной способности.При оптимизации производства цифровые технологии используются для просмотра процессов и устранения узких мест в режиме реального времени. Затем проблемы могут быть быстро решены для повышения эффективности, сокращения запасов и увеличения пропускной способности.
Благодаря использованию промышленного Интернета вещей производители могут получить полное представление обо всем производственном процессе. Они могут использовать полученные знания для внесения корректировок в реальном времени, чтобы поддерживать непрерывный поток готовой продукции и избегать дефектов.Машину можно дистанционно отслеживать, контролировать и регулировать с помощью данных датчиков, собранных на заводе (ах).
6-этапный подход Fujitsu к оптимизации производства
Fujitsu — не только ведущий мировой поставщик технологий, но и производитель мирового класса с многолетним опытом.В рамках собственного производства мы успешно используем технологии автоматизации Fujitsu, которые разрабатывались и совершенствовались нами в течение многих лет. Мы хотим поделиться своим опытом и знаниями с производителями по всему миру, помогая им внедрять технологии автоматизации для повышения их производительности.
Почему выбирают производственную технологию Fujitsu?
Мы — опытный производитель и поставщик ИТ-услуг с проверенным опытом предоставления производственных ИТ-решений, которые повышают эффективность, сокращают запасы и увеличивают пропускную способность.Внедряя наши технологии, производители по всему миру могут увеличить производительность производственных линий на 25%. Наши производственные решения:
- улучшить вид сквозной операции
- обеспечивает уведомление о проблемах и неисправностях в режиме реального времени
- улучшить поддержку анализа первопричин
- улучшить управленческую отчетность и сравнительный анализ по всему миру
Благодаря нашим комплексным услугам мы обеспечиваем полную поддержку жизненного цикла решения:
- Установка — мы проведем обследование объекта и адаптируем наше стандартное производственное решение к вашим уникальным потребностям.
- Машинное обучение и решение — с помощью инструментов машинного обучения наши специалисты по обработке данных создают алгоритмы, развернутые в облаке, для анализа ваших данных и получения информации. Они представлены через панель управления, уведомления о сообщениях и интеграцию с корпоративными системами.
- Application Services — мы работаем и обслуживаем приложения, в том числе разработанные для удовлетворения ваших конкретных потребностей.
- Профилактическое обслуживание — это часть нашего облачного решения для оптимизации производства с несколькими арендаторами, которое:
- собирает данные в реальном времени с машин
- управлять устройствами
- обновляет цифрового двойника статусом и данными аналитических алгоритмов
- визуализирует цифрового двойника и действует посредством интеграции с корпоративными системами
Преимущества включают сокращение времени простоя и уменьшение затрат на техническое обслуживание и капитальные затраты.
В число предлагаемых нами производственных ИТ-услуг входят:
Служба Fujitsu ManageNow®
- Предварительно настроенные сервисные решения для управления ИТ-операциями в гетерогенных ИТ-инфраструктурах.
- Решения, ускоряющие внедрение и настройку эффективной операционной среды ИТ.
- Пакеты услуг с фиксированной ценой (программное обеспечение, услуги по развертыванию и поддержка) только с 1 номером заказа.
Интеллектуальная приборная панель Fujitsu
- Предоставляет окно оптимизации производства — цифровые технологии используются для просмотра процессов и устранения узких мест в режиме реального времени.
- Обеспечивает повышение эффективности, сокращение запасов и увеличение пропускной способности.
- Обеспечивает единое представление в реальном времени всей глобальной операции с управленческой отчетностью и подробным описанием машин и процессов, поддерживающих анализ первопричин.
Оптимизация производственного процесса с целью повышения эффективности и снижения рабочей нагрузки
Когда специалисты по эргономике, ViveLab, получили заказ от Secret Hungary Ltd.результаты исследования на их производственной линии имели далеко идущие последствия. Произошла не только оптимизация производственного процесса, но и их анализ повлиял на реорганизацию рабочей станции и реорганизацию рабочего процесса. В результате эффективность и производительность резко повысились, что помогло фабрике сократить расходы. Узнай как:
Основная цель исследования заключалась в том, чтобы проверить эффективность рабочих нагрузок, а также влияние процессов на персонал и устранить узкие места — все для обеспечения соответствия стандарту EN 1005-4.
На протяжении всего проекта команда проверяла рабочие инструкции, отслеживала рабочие процессы, фиксировала, как рабочие перемещались и взаимодействовали с конвейерной линией. Он также измерял время цикла для каждой задачи, чтобы получить полное представление об операции.
Затем результаты опроса и рекомендации по оптимизации были смоделированы и проанализированы с помощью программного обеспечения ViveLab Ergo, что позволяет сравнивать существующие и запланированные рабочие процессы.
Это проводилось в 4 этапа:
ШАГ 1: ОТБОР, I.E. ОЦЕНКА ЭРГОНОМИЧЕСКОГО ВОЗДЕЙСТВИЯ
Во время проверки рабочие станции на производственной линии были классифицированы в соответствии с интенсивностью рабочих нагрузок, а также серьезностью воздействия на здоровье и сопутствующими рисками.
Этот первый этап помог команде ViveLab как можно быстрее оценить общее состояние производственной зоны, увидеть, где проблема является наиболее острой и где корректирующие меры будут наиболее эффективными, чтобы их можно было определить по приоритетам.
Это было рассмотрено с клиентом, и они согласовали выбранные области для дальнейшего исследования с использованием оборудования для захвата движения и анализа с помощью ViveLab Ergo.
ШАГ 2: ЗАХВАТ ДВИЖЕНИЯ СЕНСОРНЫМ ОБОРУДОВАНИЕМ
Движение рабочих на сборочной линии фиксировалось 17 беспроводными инерциальными датчиками Xsens, прикрепленными к их телам. В отличие от оптических датчиков, для инерционного захвата движения не требуется система камеры, и, уникальная для технологии Xsens Motion Capture, электромагнитные волны не искажают данные.
Датчики можно было откалибровать быстро и легко, не мешая производственному процессу, и не препятствовало физическим нагрузкам и не влияло на них — это означало, что рабочие могли двигаться естественно, что приводило к записи, которая точно отражала типичный рабочий день.
ШАГ 3: МОДЕЛИРОВАНИЕ И АНАЛИЗ VIVELAB ERGO
На основе планов этажей команда построила цифровую модель линии предварительной сборки. После создания среды они создали виртуальных человеческих персонажей и назначили каждому персонажу соответствующие файлы движений, которые ранее были захвачены с помощью костюмов Xsens. В результате у них была рабочая модель сборочной линии с движением, связанным с производственной деятельностью на ней.
Благодаря инерционному захвату движения встроенные методы анализа также могут обнаруживать критические движения и позы, которые могли не замечаться ранее или которые могли оставаться скрытыми из-за потенциальных эффектов экранирования.Затем ViveLab экспортировал аналитические отчеты, в которых были выделены позиции — с соответствующими углами и с точностью до сотых долей секунды — которые необходимо отрегулировать, чтобы снизить нагрузку на сотрудников.
Программа оценивает позы сотрудников в соответствии с несколькими встроенными инструментами эргономического анализа: методами RULA, OWAS, NASA-OBI, стандартами ISO 11226, EN 1005-4, диаграммой спагетти и тестом достижимости. Программа проверяет, не превышает ли нагрузка на каждую часть тела допустимый предел.
Команда исследовала различные виды вредных для здоровья позы, которые встречаются часто, и проанализировала движения, которые могут значительно замедлить рабочий процесс. Изучая движения, они определили движения, которые не были необходимы для успешного выполнения задачи, и искали способы их избежать. В результате время цикла было сокращено, и появилась возможность ускорить конвейерную ленту.
Одной из самых больших проблем, выявленных в отчете, была нехватка места.Следовательно, было трудно получить доступ к различным и открытым частям рабочих станций, что влияло на способность исследователя найти подходящее место для контейнеров с припасами. В результате сотрудники затрудняли передвижение друг друга, а инструменты и приспособления становились громоздкими.
ШАГ 4: ТЕХНИЧЕСКИЙ ДИЗАЙН, ВИРТУАЛЬНАЯ ПРОВЕРКА
Отчет, который был экспортирован из программного обеспечения, представил перемещения, которые были признаны физически сложными или которых можно было избежать.Этот отчет, основанный на точных и объективных измерениях, предоставляет важные данные для группы разработчиков, состоящей из инженеров и экспертов по эргономике. Исходя из этого, нашими специалистами был разработан план мероприятий, включающий несколько индивидуальных, организационных и технических предложений. Затем группа записала движения в новом макете и смоделировала новые рабочие процессы.
Виртуальная проверка без прототипа перед внедрением, с Xsens MVN Analyze
Вместо того, чтобы работать на двух больших верстаках, как это было раньше, каждый сотрудник работает за своим регулируемым по высоте столом на новой линии предварительной сборки.Это позволяет им работать за столом, подходящим для их собственного роста. Преимущество этого решения заключается в том, что рабочие могут выполнять свои задачи с комфортом, снижая при этом утомляемость. Таким образом, мышцы шеи, плеч и позвоночника у рабочего менее напряжены.
На основе анализа компания ViveLab рекомендовала предоставить сотрудникам стул, чтобы они могли менять положение стоя или сидя — это также поддерживается столом с регулируемой высотой. Стул, который они используют, также должен иметь колеса, которые могут легко катиться ближе к контейнеру или конвейерной ленте.
Было предложено установить роликовые конвейеры между различными рабочими местами для передачи предметов, подлежащих сборке, чтобы уменьшить производственный травматизм.
РЕЗУЛЬТАТЫ ПРОЕКТА
Одним из наиболее важных эффектов, упомянутых в результате корректирующих мер, было сокращение времени цикла в блоке предварительной сборки. Появилась возможность ускорить конвейерную ленту по запросу на 15%; сокращение времени, необходимого для производства конечного продукта.Этот более быстрый производственный процесс увеличивает годовой доход компании примерно на 250 000 евро.
Благодаря реорганизации один сотрудник вместо двух может выполнять задание на АРМ по монтажу кабельной коробки. Как следствие, запасной рабочий может быть переведен в другой район, где наблюдается нехватка рабочей силы. Это позволит компании сэкономить около 15 000 евро на годовой заработной плате.
Кроме того, стало намного удобнее обеспечивать линию сырьем.Требуемая площадь рабочих мест была уменьшена с 41 м2 до 24 м2.
Компания ViveLab провела испытания модернизированных рабочих станций с программным обеспечением ViveLabErgo в соответствии с теми же методами эргономического анализа, что и в случае с исходными рабочими местами. Отчет, экспортированный из программного обеспечения, содержит подробные сведения о результатах анализа для каждой рабочей станции. В этом документе сравниваются результаты анализа RULA, однако финансовую выгоду, полученную за счет защиты здоровья рабочих, сложно определить количественно.Профилактика заболеваний опорно-двигательного аппарата также означает экономию финансовых средств, поскольку значительно сокращается стоимость дней отпуска по болезни.
Как и оригинальные рабочие станции, модернизированные рабочие станции были проверены и протестированы в соответствии со стандартами ISO 11226 и EN 1005-4. Каждый метод анализа доказывает, что переработанный рабочий процесс стал для сотрудников гораздо менее обременительным.
ЗАКЛЮЧЕНИЕ
Пример, представленный здесь, демонстрирует, как на основе результатов подробного эргономического исследования успешная реконструкция рабочей станции (или всего производственного подразделения) реорганизует рабочий процесс и может повысить эффективность всей фабрики.Даже с меньшим количеством рабочих производство идет быстрее, а производственные площади сокращаются. Однако бесценно то, что работодатель сделал все возможное, чтобы предотвратить нарушения опорно-двигательного аппарата. В результате внесенных изменений рабочие будут меньше истощены к концу смены, а также снизится риск возникновения опорно-двигательного аппарата и других проблем. Кроме того, эргономичные рабочие места помогают обеспечить безопасность и комфорт сотрудников при выполнении своих обязанностей.
Вас интересуют наши решения? Пожалуйста, нажмите кнопку ниже, чтобы связаться с нами.